事例紹介動画
お客さまPROFILE
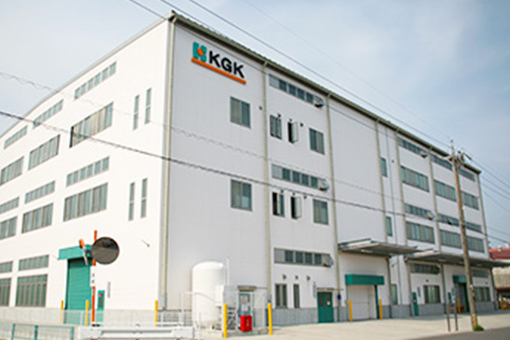
軍需用のネジ製造を事業として、1944年に創業された株式会社ギフ加藤製作所さまは、戦後、自動車産業の発展・拡大に合わせて、自動車関連部品の製造にシフト。精密自動車部品および自動制御機器部品のメーカーとして「品質至上」を基に、加工技術の研究開発を通じて高品質、低コストの商品づくりに取り組んでいます。
現在は、岐阜県内に8工場と中国に1工場の生産ネットワークを有し、大手自動車部品メーカーからの需要に高い技術力で応えています。
プロジェクトメンバー
ギフ加藤製作所
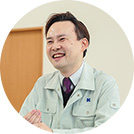
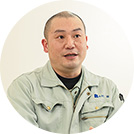
中部電力ミライズ
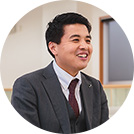
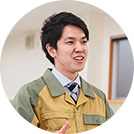
(注)所属は2021年1月取材当時
index
生産拡大の一方で、
現場課題の解決が追いつかない
というジレンマ
ギフ加藤製作所さまでは、自動車メーカーの旺盛な需要に伴い、生産量は年を追うごとに増加しています。そうした生産拡大の中、各工場ではさまざまな課題を抱えるものの、体制整備が追いつかず、課題解決が進まないというジレンマに陥っていました。また、省エネ活動にも取り組んでいたものの、目立った効果は得られていませんでした。
中部電力ミライズは、ギフ加藤製作所さまに対し、従来のようなエネルギーコスト削減に対するはたらきかけだけでなく、お客さまと一緒にさまざま観点から課題解決を進めていく、生産革新コンサルをご提案をしました。これは、さまざまな製造メーカー様に、中部電力ミライズを電力会社の枠を超えた、総合的なビジネスパートナーとして選んでいただくための新たなアプローチです。
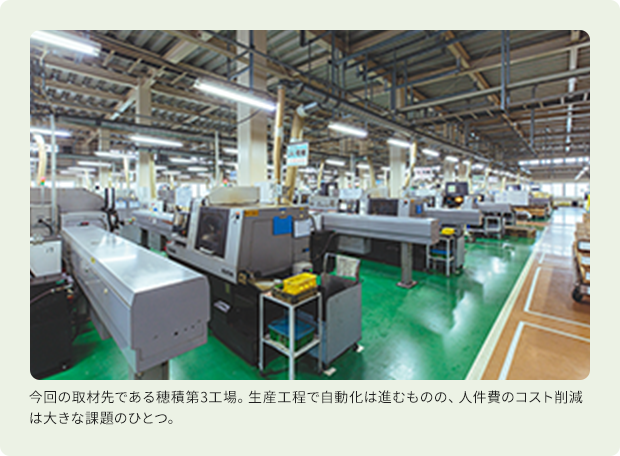
現場調査で具体的な
課題をピックアップし、
改善ターゲットを絞り込む
今回の生産革新コンサルでは、ギフ加藤製作所さまの事業背景と現状をもとに、各工程のリードタイム短縮化による生産性の安定化、コスト削減による収益の向上を図ることの必要性をご説明しました。.1~0.01mmの超微粒の帯電した気泡によって、さまざまな汚れを効果的に洗浄する新技術でした。
そのためには、まず各工程での具体的な課題をしっかり洗い出すことが重要。時にはお客さま自身が気づいていないこともあります。そのため、中部電力ミライズでは、本店と岐阜営業本部で5名のプロジェクトチームを組み、穂積第3工場の現場を数日間にわたってくまなく見て回り、調査させていただきました。
同時にギフ加藤製作所さまにヒアリングを重ねた結果、「放電加工製品の検査工程の自働化」が改善ターゲットのひとつとして浮上。自働化による人件費の削減を検討することになりました。
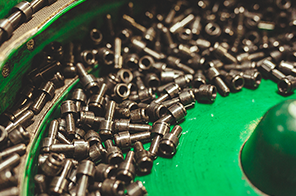
工場内で切削されてできた製品。まだ穴が開いていない状態
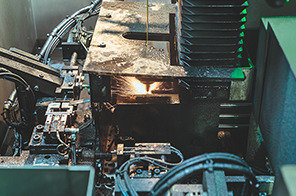
放電加工機で十字状に貫通穴が開けられる
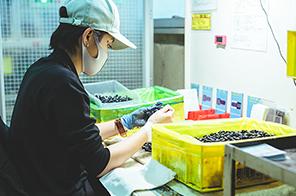
人の目と手でひとつづつ入念に検査している
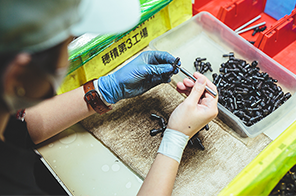
極小な穴の貫通有無はピンゲージを差し込んで確認
中部電力が培ってきた
画像検査・解析技術を応用した
「自働検査装置」の開発を提案
この検査工程は、放電加工機で製品に十字に開けた、2mmの極小な貫通穴の状態をチェックするもの。製品は自動車のアイドリングストップ機能に使われるため、自動車メーカーからはより高い精度が求められ、容認される誤差は僅か±数ミクロン。そのため、検査員による検査精度とスピードに匹敵するような自働検査システムの構築は非常に難しく、これまで手をこまねいていたのです。
中部電力ミライズは、ギフ加藤製作所さまから検査対象製品をお借りし、プロジェクトメンバー間で協議を重ねた結果、長年にわたり中部電力グループで培ってきた、各種の画像検査・解析技術が応用できるのではないか、と立案。ギフ加藤製作所さまに、自働検査システムの概要・仕様をご提案しました。
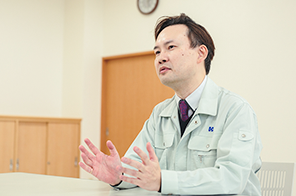
専門外の電力会社にできるのだろうか、と当初は半信半疑だった加藤さま(ギフ加藤製作所)

ギフ加藤製作所
加藤さま
「できる範囲で協力はしますが、“できるものならどうぞやってみてください”というくらいの気持ちでした。今思えば失礼な話ですけど(笑)」
実は、加藤さまの前職は、業務用特殊カメラメーカーのエンジニア。撮影や画像処理に対する高い知見をお持ちであり、検査装置の専門メーカーでも中々作れないものを、電力会社である中部電力ミライズにできるのだろうか、と半信半疑だったそうです。
限られた設置スペースに
新方式の検査システムという
設計課題
今回の画像検査に応用した技術は、電力事業のさまざまな用途で活用するために、中部電力グループが長年にわたり、独自で開発してきた技術をベースにしたもの。とはいえ、そのまま適用できるわけはなく、設計・開発は試行錯誤を繰り返しました。

中部電力
ミライズ
「せっかく課題解決の機会をいただいたので、何とか良い結果を出したいとスタートしました。私は営業という立場ですが、弊社の技術開発メンバーに一任するのではなく、かなり踏み込んだ議論を重ねました」
自働検査装置は他社メーカーにも存在しますが、放電加工品の穴径を画像解析技術を用いて検査する方式は、これまでにない新しい発想のもの。そして、検査する製品の穴は十字状に二本貫通しているため、1台のカメラで、短時間で判定するには、製品をつまみ上げて360°以上回転させて撮影する必要があると考えました。
また、工場内には自働検査装置を設置するスペースが限られており、検査員の作業のしやすさ(自働化した場合も、再検査のための人員は1名必要)も考慮しなければならないため、サイズと仕様の両面をクリアする設計に苦心しました。
判定結果については、良品と不良品という二択にするのではなく、どちらか決めかねる「グレー判定」の要素を取り入れることで、設定した閾値(いきち)ギリギリの製品は再検査品に振り分け、人的な検査との整合性を図りました。
さらに、検査精度に加え、検査スピードも重要なポイント。開発メンバーが実際に検査員の後ろで作業タイムの計測を繰り返し、最適な設定タイム(1個あたり4秒)を割り出しました。
装置設計時とフィ―ルド試験前には、プロジェクトメンバー全員でデザインレビューを実施。想定される不具合、故障要因などを洗い出し、あらかじめ対策を決めて開発を進めました。
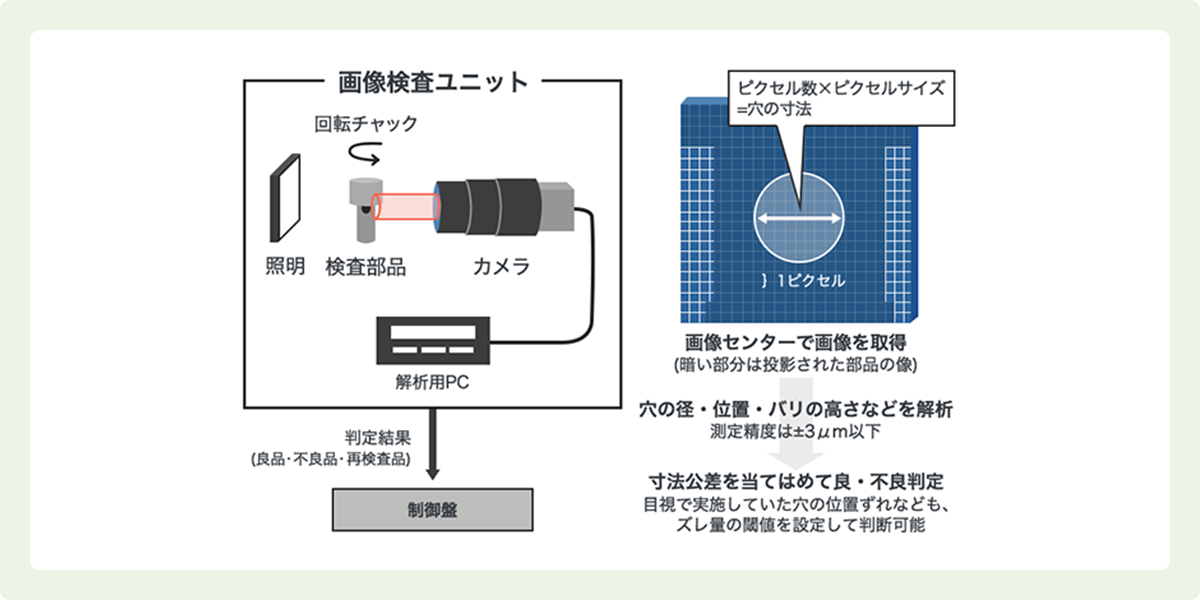
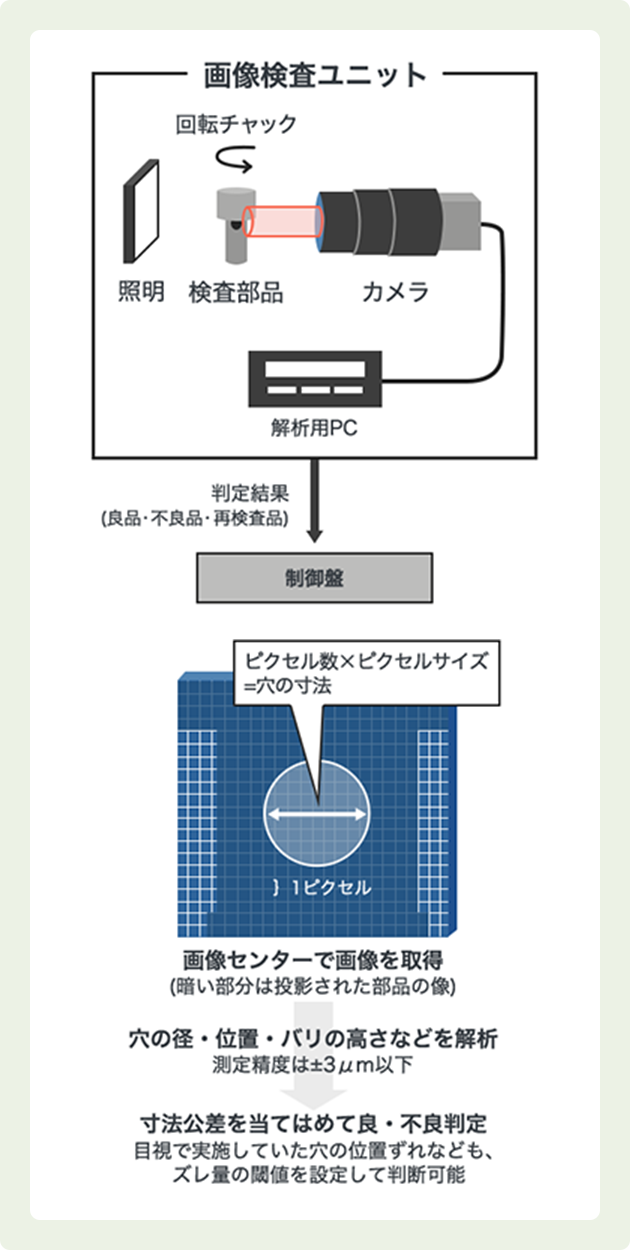
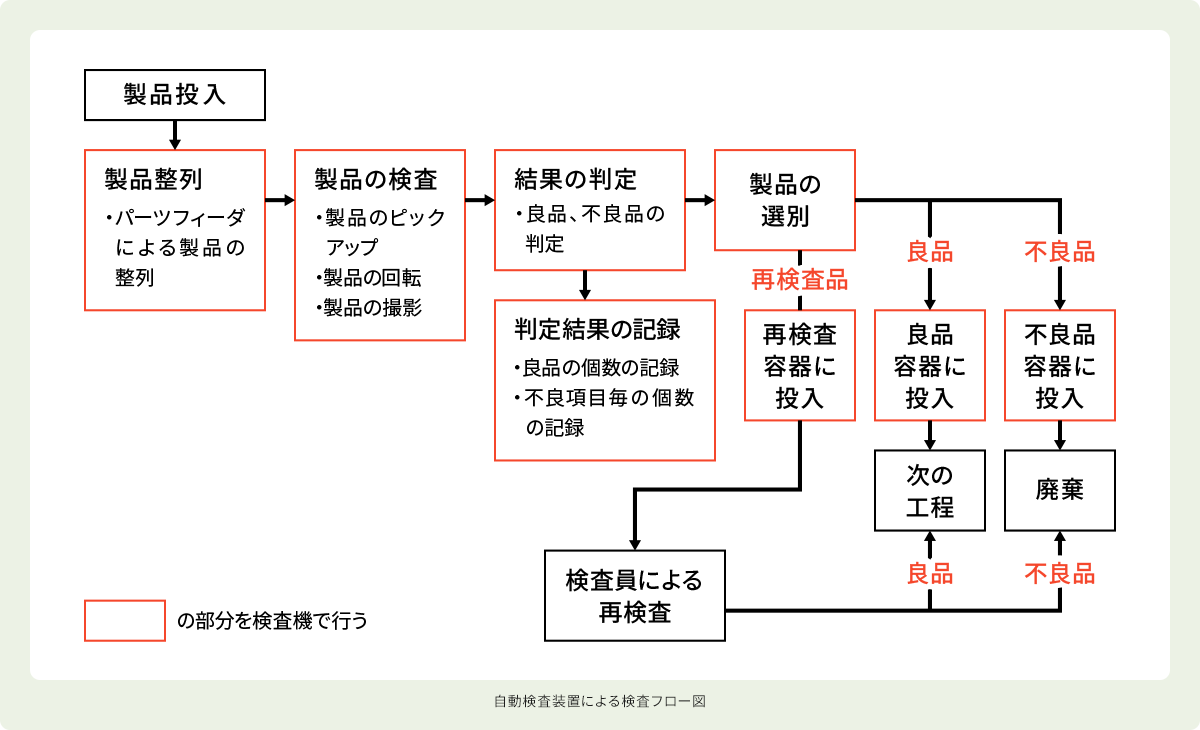
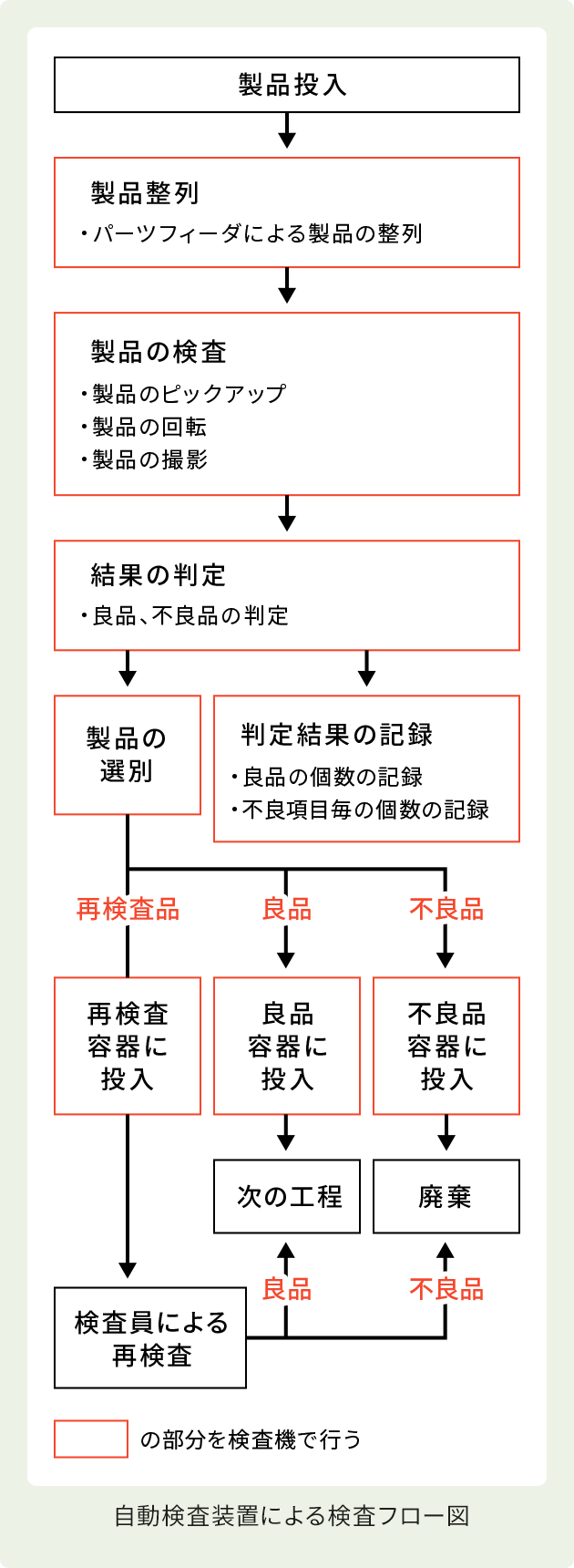
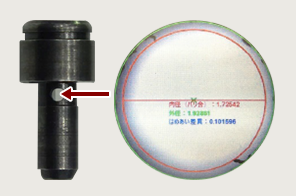
放電加工で開けられた2mmの極小な貫通穴を自働検査しなければならない
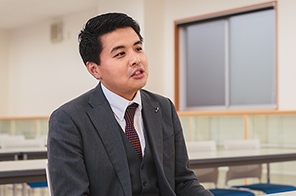
営業という立場にこだわらず、技術面でも積極的に議論したという高橋(中部電力ミライズ)
実機の試験段階では
トライ&エラーを繰り返し、
要件のクリアに苦労
中部電力グループの実験施設で開発製作された実機の試験段階では、多くの難題に突き当たりました。ギフ加藤製作所さまから試験用に良品と不良品を各1,000個ずつご提供いただき、穴径や位置、貫通の有無などの画像検査を実施。数ミクロンの精度が求められる中、当初は検査機の回転スピードが定速ではなかったことや、回転時のブレが判定に影響して数ミクロンの誤差が出てしまうなど、プログラムと機器の両面の設計見直しを迫られました。また、画像検査では、輝度(明るさ)で穴を「円」として認識する範囲を決めていますが、その境界位置しだいで判定結果も大きく変わってしまうため、確かな精度が出るように何度も検証を重ねて位置決めをおこないました。
さらに、製品の穴には、加工時に生じる「バリ」(不要な突起)が付いているものがあり、それを「円」として画像認識するかどうかも判定に影響を及ぼします。バリをバリとして、カメラに認識させるため、照明の明るさや角度を何度も変更しながら検証。ハードで対応しきれない部分は、解析プログラムを改修するなど苦労を重ねました。

中部電力
ミライズ
「検査装置の開発をしていた弊社の実験施設には、約4ヶ月間ほとんど毎週通いました。開発・試験段階での状況を随時お客さまにお伝えしながら、欲しい情報や疑問点は積極的にお尋ねし、逐一開発にフィードバックしました」
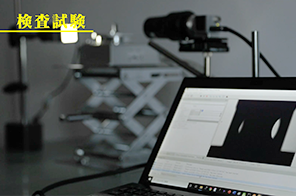
試験段階での実機の様子。さまざまな調整や見直しがおこなわれた

名古屋市(緑区)にある実験施設に岐阜から通いつめた高木(中部電力ミライズ)
現場フィールド試験で
ブラッシュアップ。
検査員の省人化に成功
動作および性能面が目標レベルに達した頃、ギフ加藤製作所さまからは、社長、生産技術部長、加藤さまに実験施設にお越しいただき、自働検査装置の確認をしていただきました。

ギフ加藤製作所
加藤さま
「そのときに形になった装置を初めて見ましたが、正直よくここまで作ったなと思いました。中々しっかり出来ていましたし、弊社の社長も“次も何か中電さんにお願いしているのか”と、早くも期待を寄せていました」
ギフ加藤製作所さまから承認を得ることができ、実際に工場に設置し、最終的なフィールド試験をおこなうことに。しかし、ここで問題が発生。検査の前工程で、製品に防錆用の油脂が想定以上に付着することが判明したのです。油脂が付着したままだと、照明の光が穴を通らず、撮影しても画像センサーが穴を認識できず、検査判定に影響してしまいます。すぐに、エアーを吹き付けて油脂を落とす機能を追加(落とした油脂を溜めるオイルパンも設置)。また、工場内には油煙が舞っているため、自働検査機を保護シートでカバーしました。迅速に対応できたのは、設計時とフィールド試験前に想定される問題を洗い出し、共有しておいたことが功を奏したのです。

ギフ加藤製作所
加藤さま
「何か起きても、すぐに対処してくれましたし、現場での細かな調整やサポートも粘り強くやっていただけたので安心してお任せできました」
フィールドテストでの最適な精度調整を終え、無事納入された自働検査機は現在本格稼働し、従来とまったく遜色ない検査精度とサイクルタイムを実現。検査員2名分の人件費コスト削減にも成功しました。
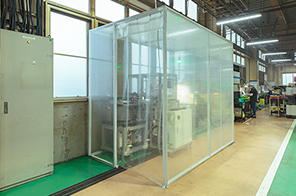
油煙保護用のシートでしっかり覆われた自働検査装置
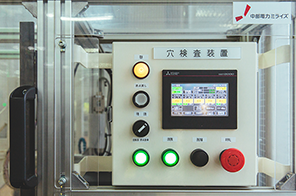
装置を制御する操作パネル
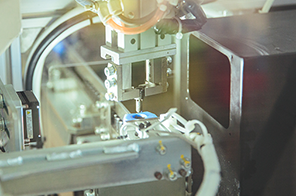
検査する製品をアームがつまみ上げ、回転させて穴を照明に向ける
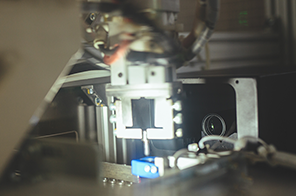
照明で照らされた穴をカメラで撮影
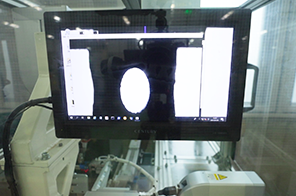
画像センサーが穴の径、位置、貫通の有無などを解析し、判定して振り分ける
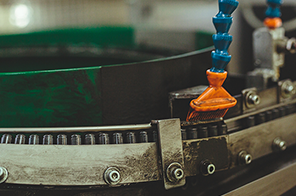
製品に付着した油脂を先にエアーで吹き飛ばす
他の検査工程や工場での
課題解決にも
今後大きな期待
今回ギフ加藤製作所さまへの生産革新コンサルのご提案の中から実現した、検査工程の自働化システム。これは、装置や設備を作ることで課題解決を図ることが当初からの目的だったのではなく、あくまでもお客さまの立場になって、最適なソリューションとは何かという視点から生まれたものです。

ギフ加藤製作所
加藤さま
「最初はそれほど期待してなかったですが、結果的に信頼性の高いものを作っていただけたと思っています。これを機に、第二、第三の課題解決もまたぜひお願いしたいですね」
中部電力ミライズは、これからもギフ加藤製作所さまをはじめ、さまざまな製造メーカーのお客さまのそばで、一緒に現場の課題解決に取り組んでまいります。
この事例で導入されている製品・技術
製品
寸法検査装置
検査、ポカヨケ、監視など、作業者が目で見て判断している工程を自働化します。お客さまニーズに合わせ、最適技術の選定から、現場環境を想定した事前検証、システム開発までご提案します。
詳細を見る
ギフ加藤製作所
加藤さま
「検査は3人体制で、目視と手作業でやっていましたから、人件費にかかるコストを何とか削減できないかと、ずっと考えていました」