お客さまPROFILE
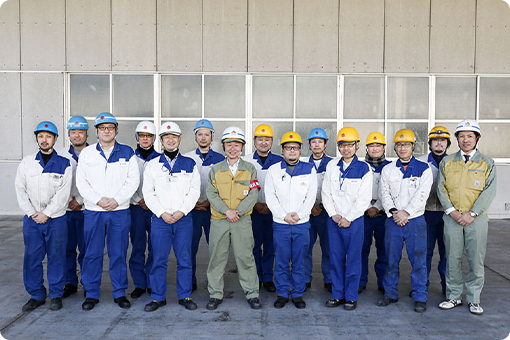
「スイフト」「ソリオ」「クロスビー」などの小型車をはじめ二輪車や船外機も手掛けるスズキ株式会社(以下、スズキ)さまは、日本を代表するコンパクトカーメーカーとして成長し、現在では各国に生産拠点を擁する“世界のスズキ”として愛されています。その中で相良工場さまは、1992年にエンジン主要部品の鋳造・加工・組立工場として操業を始め、2008年より小型車の生産を開始。
197万m2の広大な敷地にはテストコースも備え、“世界のマザー工場”として重要な役割を担っています。
プロジェクトメンバー
スズキ
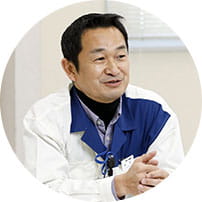
相良工場鋳造課 課長池谷 泰慶
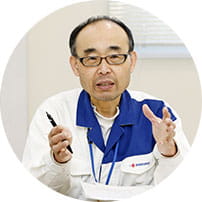
相良工場技術課谷口 隆彦
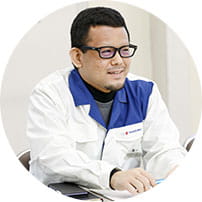
相良工場鋳造課下村 進也
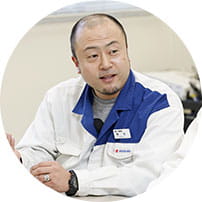
相良工場鋳造課 組長植田 泰之

相良工場鋳造課 組長榑林 広剛

パワートレイン生産技術部鋳造課青木 丈
中部電力ミライズ
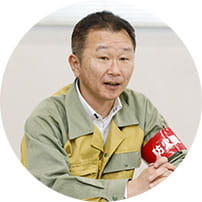
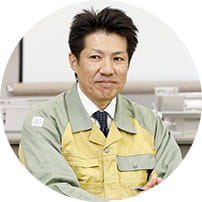
(注)所属は2020年2月取材当時
index
エネルギー使用量が多い
鋳造工程に改善のメスを
スズキさまでは「新しい手法に挑戦し、ワンランク上の技術を身につける」という方針のもと、省エネ活動でも積極果敢なチャレンジを続けています。その中で、多品種小ロット生産に対応しながらエネルギー使用の最適化を図るために浮上したテーマが、「鋳造工程の改善」でした。
溶かしたアルミを金属の型(金型)に流し込み、冷やして固めた製品を取り出す鋳造では、製品の品質安定化と金型保護のため、あらかじめ金型を加熱する必要があります。加熱方式はガスバーナ式が主流で、熱源となるLPガスを多量に消費するうえ、燃焼を維持するためのエア供給も必要です。
しかも、金型の昇温には3時間を要し、直火を扱うため危険なうえ、火力調整は作業者任せで均一化が難しいという問題もありました。
「たえず変化する生産状況に追従しながらエネルギーロスを削減するには、どうすべきか検討しなければ」。
相良工場 鋳造課のご担当者は、さっそく情報収集に乗り出しました。
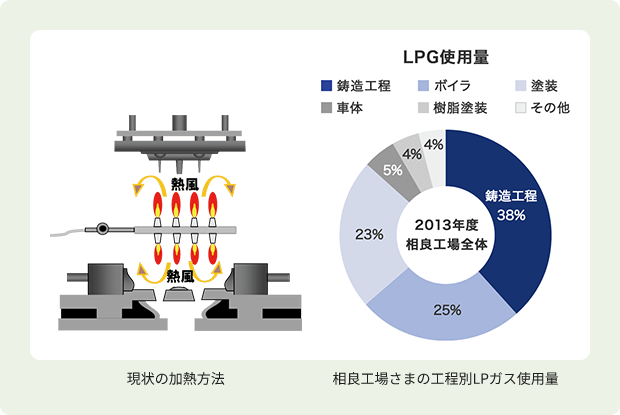
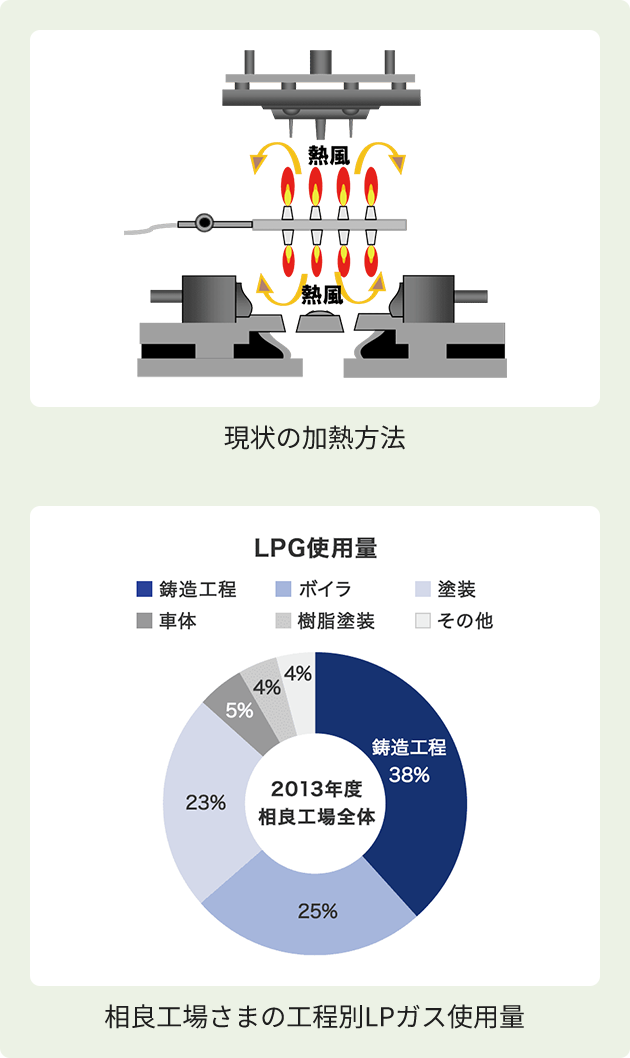
中部電力ミライズの「出前展示会」が
課題解決の入り口に
そんな折、2004年からスズキさまの各工場で多様なソリューション活動を続けている中部電力ミライズは、2013年5月に高塚工場さまで出前展示会「生産プロセス技術展」を開催しました。これは中部電力ミライズが手掛けたさまざまな技術・事例をご紹介し、生産工程に新たな改善のヒントをご提供しようと企画した催しです。
その会場に足を運ばれていた相良工場さまが目を留められたのは、赤外線ヒータでした。
中部電力ミライズが最初にご提案したのは、近赤外線の「ハロゲンヒータ」でした。近赤外線は金属への吸収率が高く、温度レスポンスにも優れていることから最適と判断したのです。
しかし、実際に金型を使って比較試験をしてみると、ガスバーナは2時間46分で目標の480℃まで加熱できたのに対し、ハロゲンヒータは3時間加熱しても460℃以上には昇温しませんでした。

スズキさま
「しかもヒータ自体が大きく、光が強く眩しいので遮光眼鏡が必要です。それで小型で人の目にも優しいヒータの提案をお願いしました」
赤外線吸収率を分析し
「カーボンヒータ」にたどりつく
試験結果を持ち帰り、中部電力ミライズの開発一体型ソリューションの場として活用している実験施設で詳しく分析したところ、原因は金型保護のため金型の表面に塗布する「塗型剤」(とがたざい)の吸収波長が影響していることが判明。塗型剤は近赤外線の吸収率が低く、思うように昇温できなかったのです。そこで、中赤外線の「カーボンヒータ」を使い、小さな金型を加熱してみると、24分で500℃まで昇温しました。


中部電力
ミライズ
「カーボンヒータの出力を高めれば、実用化の可能性は十分にあると考えました」
検証結果をスズキさまに報告し、その後、数社のカーボンヒータを比較検討した結果、時間あたりの昇温コストがガスバーナと比較し約4分の1という高効率ヒータを製造しているメトロ電気工業(以下、メトロ電気)さまを指名。3社による金型加熱器の共同開発を本格化しました。

中部電力
ミライズ
「構造的にも円筒状のハロゲンは全方向に光を放射するため、ロスが大きく眩しいのです。これに対して、カーボンヒータは面状で、上下の金型を集中的に照射するという目的に合致していました」
十数回のトライ&エラーを経て、
ついに「赤外線ヒータ式金型加熱器」誕生
試作機づくりは2013年11月に始まりました。現場での作業性を考慮し、形・大きさは従来のバーナ加熱器を基本とし、重量は10kg以下、各種金型に対応できるよう高さを調整する機能や作業者が扱いやすい「持ち手」を付けた試作機を製作。目標は「2時間で480℃の昇温と鋳造品質のカギとなる温度分布の均一性」でした。中部電力ミライズの実験施設でスズキさまの金型と同じ材料片を使い、温度分布を計測。結果は温度分布はクリアできたものの昇温に4時間を費やしてしまいました。原因は光(熱)の漏れ。試作機の側面から熱が漏れてエネルギーロスが生じていたのです。
そこで、3社が直ちに改善方法を検討し、漏れを防ぐための反射板を考案。これを取り付けた改良型を1週間で製作し、スズキさまの鋳造現場で実証試験を実施しました。そして今度は、わずか80分で設定温度に到達できたのです。
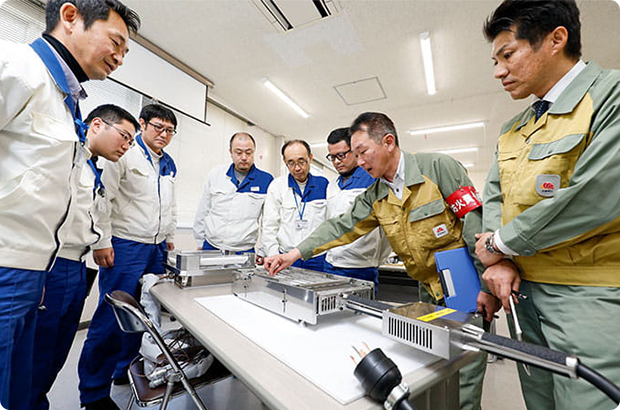

スズキさま
「この対応の早さには驚かされました。こちらは解決に向けたアイデアの提示をお願いしたのですが、まさか1週間後にそれが現物となって再テストできるとは。しかも結果は上々です。こうした俊敏さを心から頼もしく感じたものです」
最も困難だったのは、高密度の加熱に耐える筐体の設計・製作でした。加熱性能を達成するには300kW/m2の出力が必要です。当時の常識では赤外線でこのレベルの出力の場合、筐体を冷やさねばなりません。しかし、鋳造機に入れる加熱器に冷却構造を持たせるのは不可能です。そのためさまざまな材料や構造を検討。サイドフレームに耐熱性素材を採用し、さらに重量制限の数字をにらみながら最適な構造を探りました。
1週間で改良試作機を製作し、
昇温スピードを3分の1に短縮
「昇温時間の短縮」と「赤外線の放射ロス低減」に向けた改良は続きました。側面の反射板の他にも、ヒータの位置を加熱器内で限界まで下げたり、ヒータランプを保護する格子カバーを、ランプを遮らないよう平行に配置。さらに加熱器を各種の金型に使えるように高さ調整できるラベリングボルトを取り付けるなど、改良を加えては十数回のトライ&エラーを重ねました。
こうした努力を積み重ねた末に、2014年3月、目標数値をすべてクリアし、世界のどこにもない「赤外線ヒータ式金型加熱器」が完成したのです。
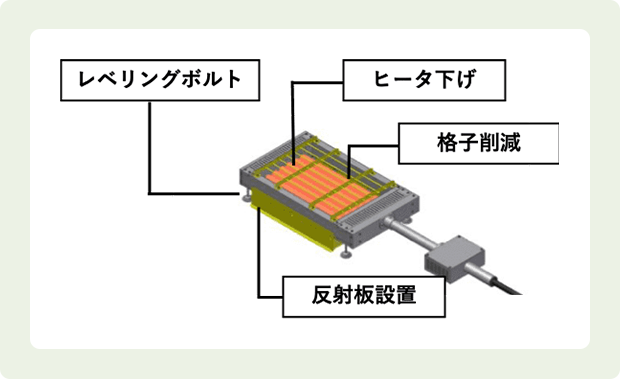

スズキさま
「テストをおこなうたびにもっと早く温度を上げたい、温度分布を均一にしたい、エネルギー効率を上げたい。そして何より、作業者が使いやすいものにしたいという無理難題を申し上げ、それを自分事として常に前向きに取り組んでいただき、とても感謝しています」

スズキさま
「失敗もありましたが、中部電力ミライズさんもメトロ電気さんも原因をしっかり究明し、次回に必ず解決策を提案していただける。その積み重ねと相互の信頼関係があったからこそ成功につながったと思います」
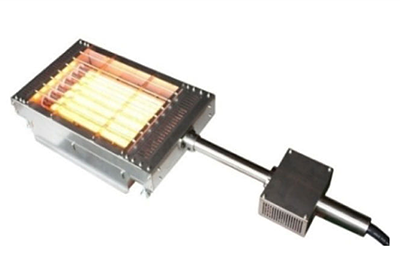
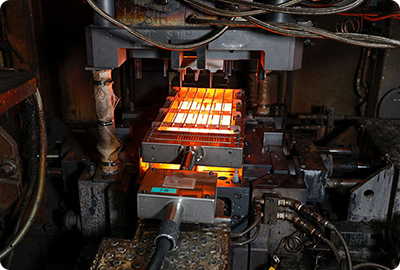
エネルギー使用量を
大幅に削減し、
省力・良品率・職場安全も向上
金型加熱器の熱源をガスバーナから電気ヒータに転換したことで、鋳造工程にさまざまな効果をもたらしました。
金型加熱器の熱源をガスバーナから電気ヒータに転換したことで、鋳造工程にさまざまな効果をもたらしました。
(1)エネルギー使用量の削減
・LPガス使用量、エア使用量がゼロに
・設定温度までの昇温時間を72%短縮(180分から50分に)
・金型加熱に要する総作業時間を32%短縮(4,746時間/月から3,211時間/月に)
・鋳造工程のエネルギー使用量は58%削減(原油換算20.8kℓ)
・CO2排出量を62%削減(77.5t-CO2/月から29.5t-CO2/月に)
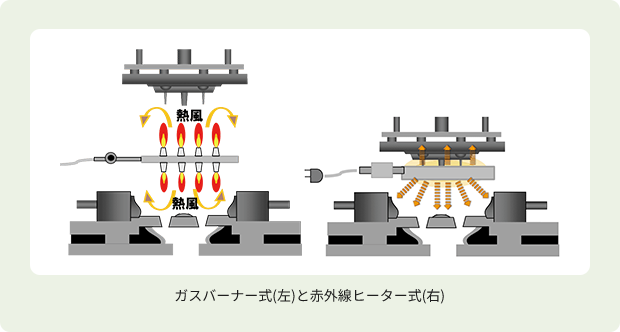
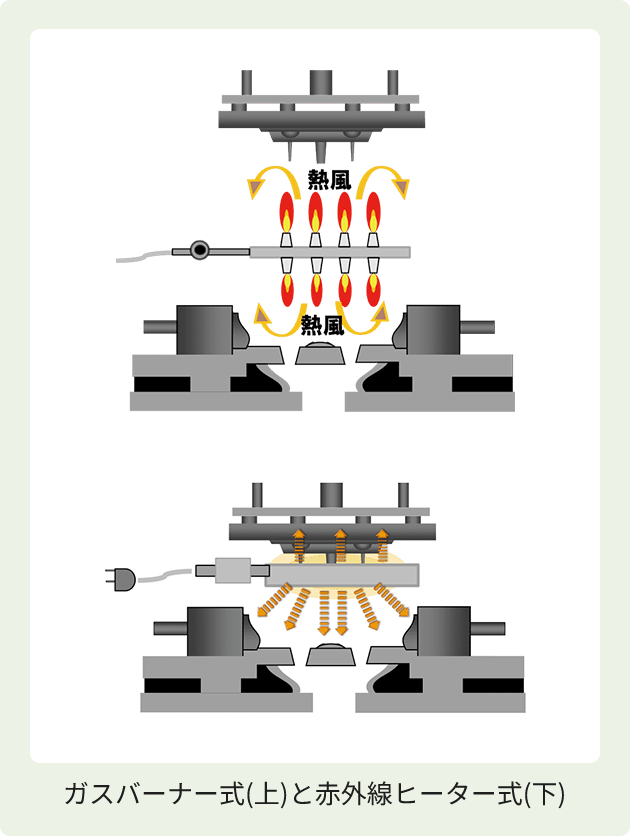
(2)大幅な省力化
ガスバーナ式では、作業者が温度を監視しながら燃焼レベルを調整する必要がありましたが、赤外線ヒータによる温度制御の自動化により不要になりました。また、立ち上げ加熱や休憩時に保熱状態を保つため、金型の突起部が過熱となり溶損するリスクも大幅に減り、始業時や1日3回おこなっていた溶損点検・補修作業を廃止できました。
さらに、従来は金型に施す塗型剤の寿命は700ショット(注)が限界でしたが、過熱による著しい焼損が防止でき、1,200ショットに長寿命化。
ほかにもガスバーナの熱による金型本体や周辺部品のトラブルもほぼ解消され、作業員の省力化を図れました。
(注)鋳造回数
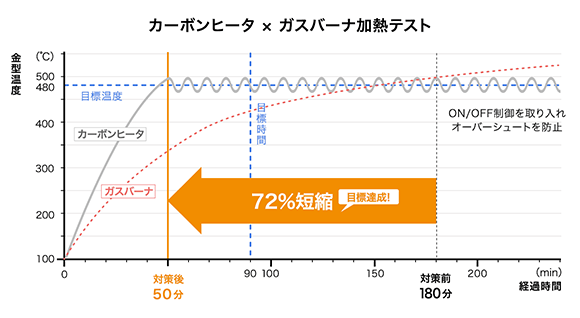

(3)良品率の向上
鋳造製品は温度分布が品質に大きな影響を及ぼします。ガスバーナの場合は、温度分布にムラが生じていましたが、赤外線ヒータはムラなく加熱でき、さらに温度の自動制御とも相まって、製品の良品率が飛躍的に向上しました。
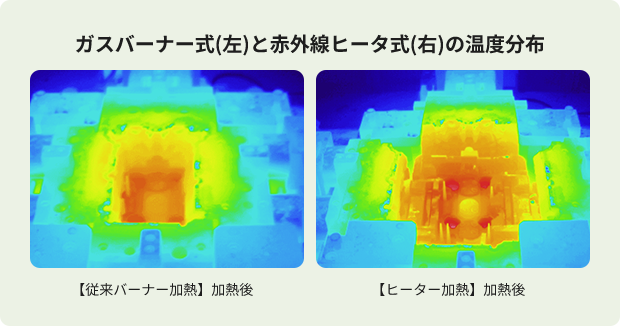
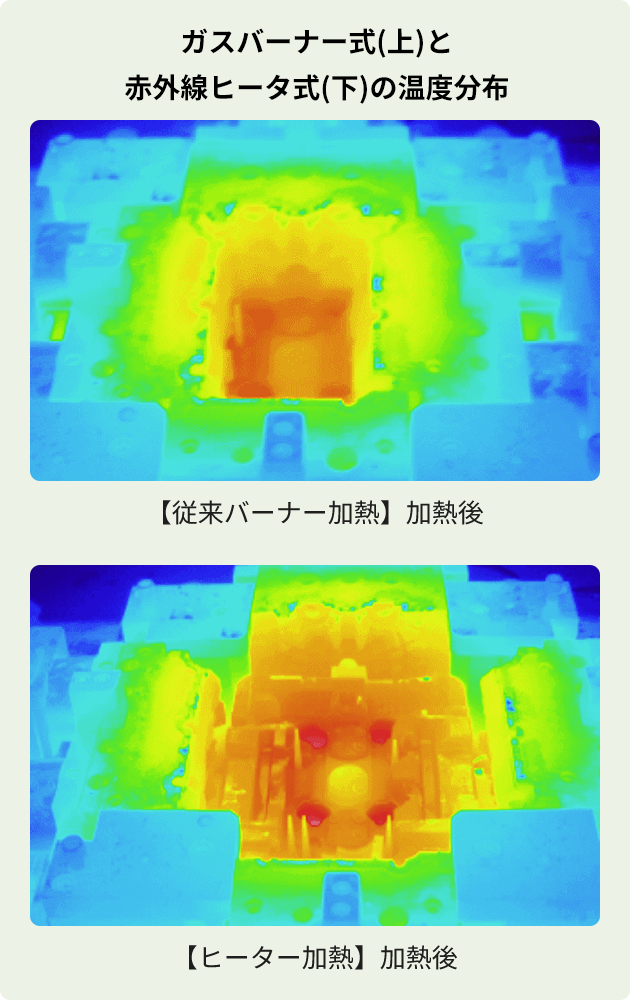
(4)職場環境の改善
ガスバーナでは直火を扱うため火災リスクがありましたが、赤外線ヒータの切替えでこれを解消。また、カーボンヒータは輻射熱が少ないため、夏場の熱気も抑制されました。

スズキさま
「シリンダヘッドの鋳造工程では、一人が4台の鋳造機を操作します。どうしても熱がこもり、他工程と比べて5℃ほど高く、夏場は45℃に達することもありました。それが今では暑さ指数が改善し(29℃から27℃)、作業者の集中力維持につながっています」
そして、2016年1月、プロジェクトチームに朗報がもたらされました。今回の取り組みが2015年度「省エネ大賞」で「資源エネルギー庁長官賞」に選ばれたのです。
金型加熱器の標準として、国内や
海外の生産拠点へ幅広く展開
今回開発した赤外線ヒータ式金型加熱器を標準とし、国内だけでなく海外生産拠点にも導入が進められています。さらに、アルミ溶湯を金型へ充填するために必要な中間タンク「サブストーク」の保温にもガスバーナを使ってきましたが、赤外線ヒータに切替えたことによりガスの管理がなくなり、まさにオール電化。省エネ・品質・安全のメリットも得られると期待されています。

スズキさま
「当社はインドやインドネシアにも拠点があり、日本より暑い環境で作業をしています。その点、この加熱器は作業環境の改善に効果的で、作業員の技能に頼らなくても品質向上が図れ、海外生産拠点にも最適で、金型加熱器の標準モデルとして海外工場に順次導入していっています」

スズキさま
「工場ではさまざまな場面で火が使われており、どのように減らしていくかが大きなテーマです。中部電力ミライズさんには引き続き協力をいただきたいと思っています」

中部電力
ミライズ
「今回のプロジェクトでは、現場の方々の意見を伺いながら一緒に改善できたことに大きな意義があると感じています。完成したら終わりではなく、良好な関係を継続しながら多方面でお役に立ちたいと願っています」
スズキさま
「赤外線ヒータのエネルギー密度が高いことに注目し、金型加熱器の熱源として使えるかもしれないと考えました。そこですぐに、中部電力ミライズさんに相良工場の鋳造工程を見ていただき課題や要望を説明、金型加熱器の提案をお願いしたのです」