お客さまPROFILE
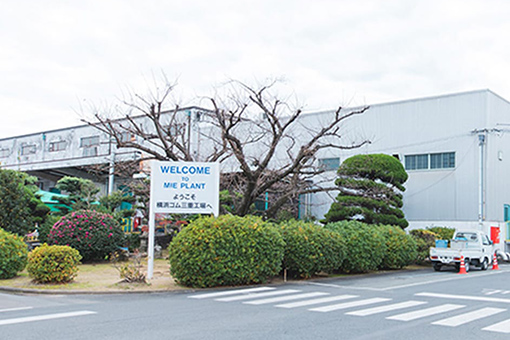
横浜ゴム株式会社さまは1917年に創立され、時代を先駆ける製品を数多く生み出してきた総合ゴムメーカです。売上高の80%を占めるタイヤ事業では国内4工場、海外9工場を展開し、世界のタイヤ市場におけるシェアは第8位。
今回の取材先である三重工場さまは1944年に操業開始。ナゴヤドーム5.5個分にも及ぶ敷地面積を有し、トラック・バス用タイヤを中心に製造する国内主力工場のひとつです。
プロジェクトメンバー
横浜ゴム
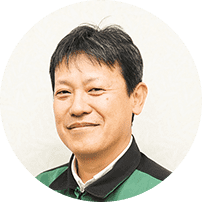
工場長森本 剛央
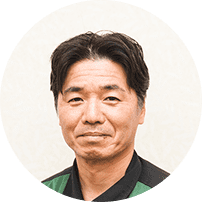
設備課長兵頭 幸博
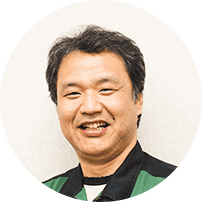
設備課 電気改善技士田所 敏彦

設備課 ボイラー作業長中村 圭介
中部電力ミライズ

法人営業部赤坂 千春
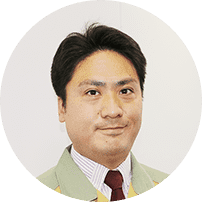
三重営業部石川 佳宏
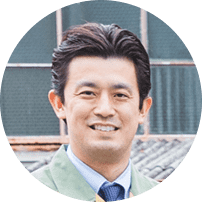
三重営業部鳴神 慎行
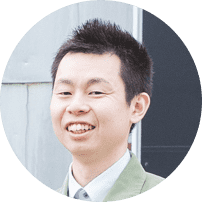
三重営業部宮澤 宏明
(注)所属は2019年12月取材当時
index
蒸気式加熱による
ダイス(押出用金型)予熱の
改善が課題に
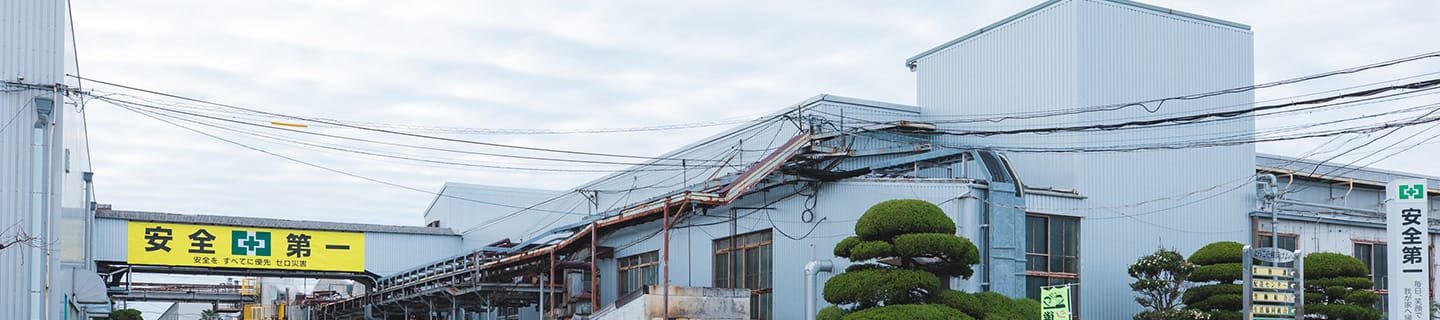
横浜ゴムさまは、創立100周年(2017年)に向けて、全社一丸で環境経営を推進していました。三重工場さまでも「毎日コツコツエコ活動(CO2 CO2 ECO)」をスローガンに省エネ活動に取り組み、設備や方法、材料、そして人を柱に工場内のあらゆる部分から省エネの可能性をピックアップ。タイヤ製造における「押出工程(タイヤと踏面の接地面のゴムを押し出す工程)」で使われているダイス(押出用金型)の予熱方法の改善がそのひとつとして挙がりました。
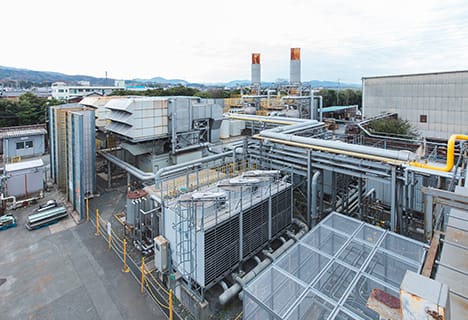
三重工場の主要熱源は、コジェネレーションシステムも組み合わせた4基の蒸気ボイラー(ガス式)。その省エネ対策が大きな課題。
従来、ダイスの予熱には蒸気式の加熱装置を使用していましたが、装置や配管からの放熱、蒸気漏れによる熱ロスが問題になっていました。また、予熱時間が30分程度かかるため、ライン停止時も加熱しておく必要があり、省エネ性向上とCO2削減が課題だったのです。
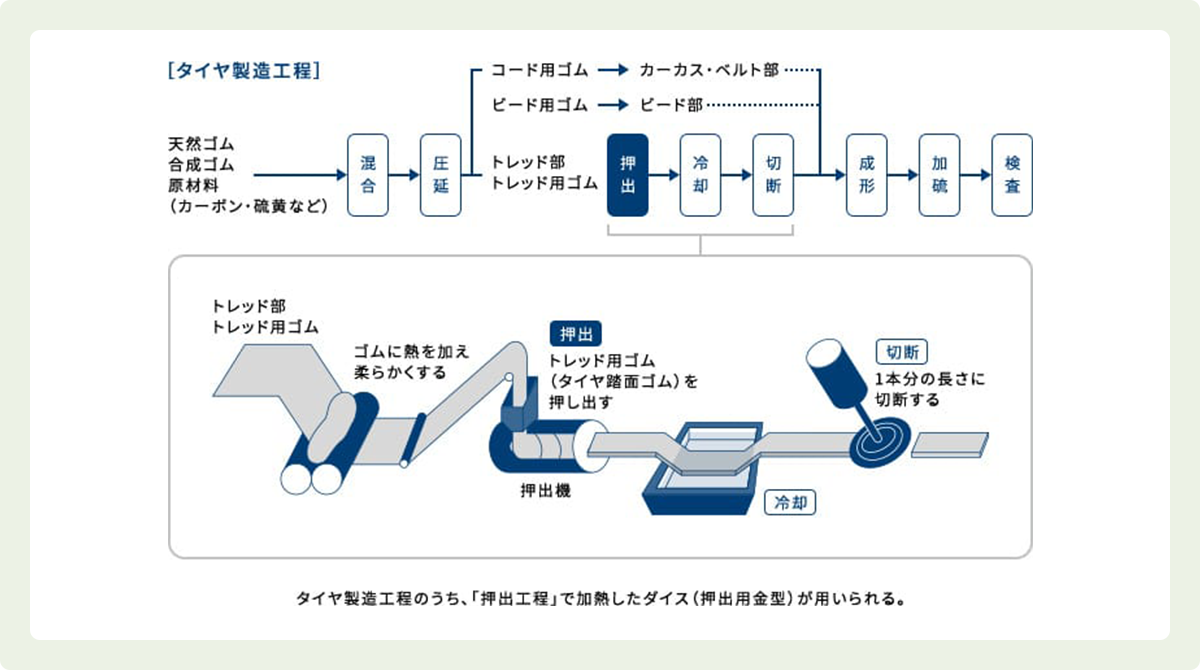
「出張加熱技術展示会」を
ご提案し、
中部電力ミライズとして初開催
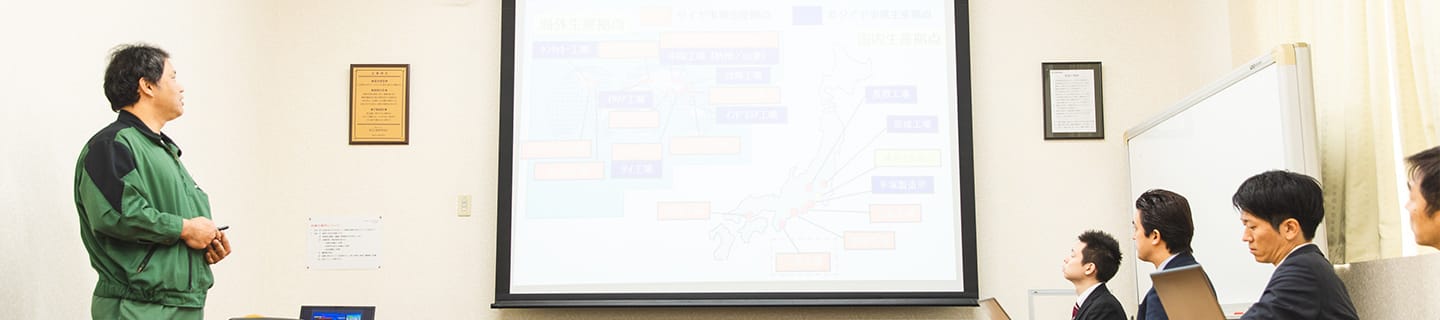
一方、中部電力ミライズでは産業分野のお客さまを対象に、既存技術では対応できない課題やニーズに対し、技術開発から一丸となって取り組む「開発一体型SO(ソリューション)」をスタートしていました。これは生産性や品質向上などお客さまが抱える経営課題を、従来の電力会社の枠を超えて共に解決していくプロジェクトです。
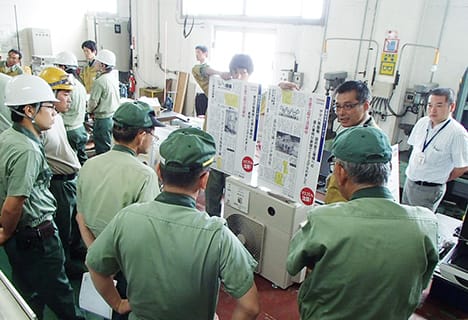
中部電力ミライズとして初めて開催した「出張加熱技術展示会」。製造現場のニーズ発掘の貴重な機会になった。
三重工場さまの省エネ活動への取り組みをお聞きする中、中部電力ミライズではその一環として課題やニーズを直接伺うため、2013年9月に同工場での「出張加熱技術展示会」の開催をご提案しました。個別のお客さまのもとに出向いておこなうのは中部電力ミライズとしても初めての試みであり、「ヒートポンプ」「IH」「過熱水蒸気」「赤外線」を用いた加熱技術を幅広く展示・実演。準備や段取りに苦心したものの、当日は若い方からベテラン、そして他工場の設備関係者まで40名を超す方々にご参加いただきました。
「私たちはタイヤ製造のことしか知らないので、幅広い産業分野に対する情報や技術を持っている中電さんの展示会はたいへん有意義でした。参加した現場スタッフからは、実演もあって分かりやすかったという声も多かったですね」(三重工場 設備課 電気改善技士 田所さま)。
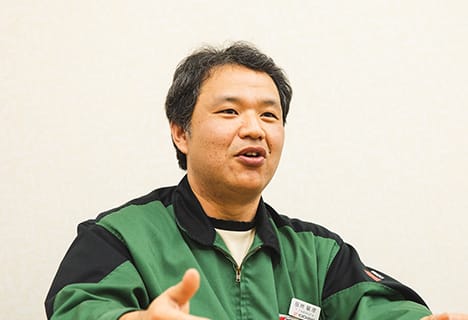
IH加熱装置導入に向け、中心的役割を担った設備課 電気 改善技士 田所さま。
IH技術を活用した
新たな加熱装置の開発がスタート
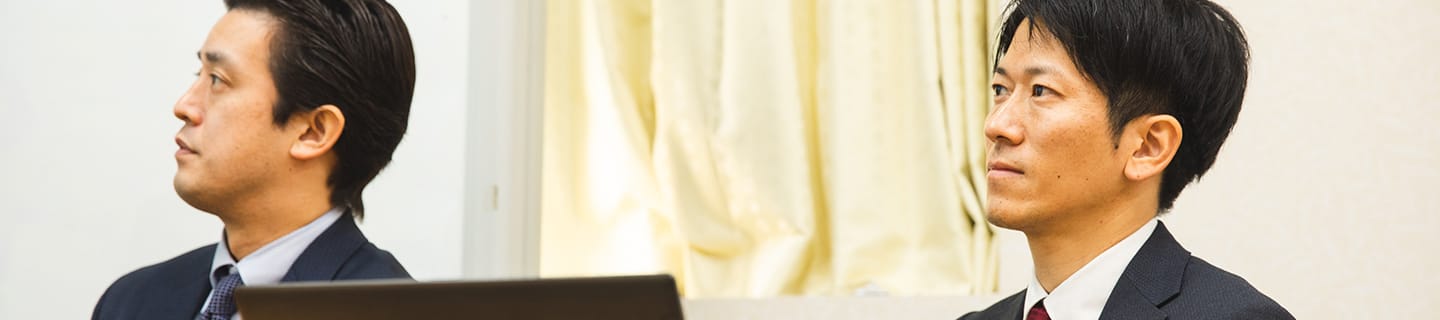
出張加熱技術展示会の終了後、三重工場さまではIHの急速加熱の技術がダイスの予熱に活用できるのではないか、という意見が浮上。しかし、これまで生産工程でIH式の設備を導入したことが無かったため具体的な方策が分からず、中部電力ミライズにご相談をいただきました。
三重工場さまの具体的な課題と要望をヒアリングし、そこで提示された要件は「ダイスの加熱時間は5分以内」「試作・検討期間は2ヶ月以内」「機器コストは投資回収3年以内」というかなりシビアなものでした。


三重工場さまの課題解決にあたったのは、石川(中部電力ミライズ三重支店:当時)、赤坂(中部電力ミライズ本店)を中心としたチーム。三重工場さまからダイスの現物をお借りし、三重支店や実験施設で試作・検証を開始しました。
三重工場さまの要件をクリアするため、電源にIH調理器などに使われる汎用インバータを採用。
IH用コイルの試作には入手・加工がしやすく、電磁誘導の影響を受けない段ボールを用いることで、コスト抑制と開発リードタイム短縮を目指しました。
「産業用インバータでは高額になるため投資回収ができません。コイルの試作もメーカに依頼していると時間が掛かりますし、途中段階での調整や手直しも難しいので柔軟な方法、しくみを考え出しました。」(赤坂)。
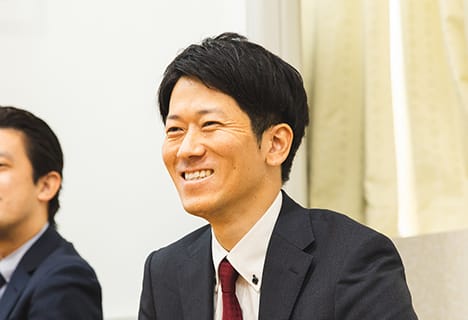
赤坂は研究所で度重なる試作・検証を技術面でサポートした。
内製化により
試作・検討期間の
超短期化を実現
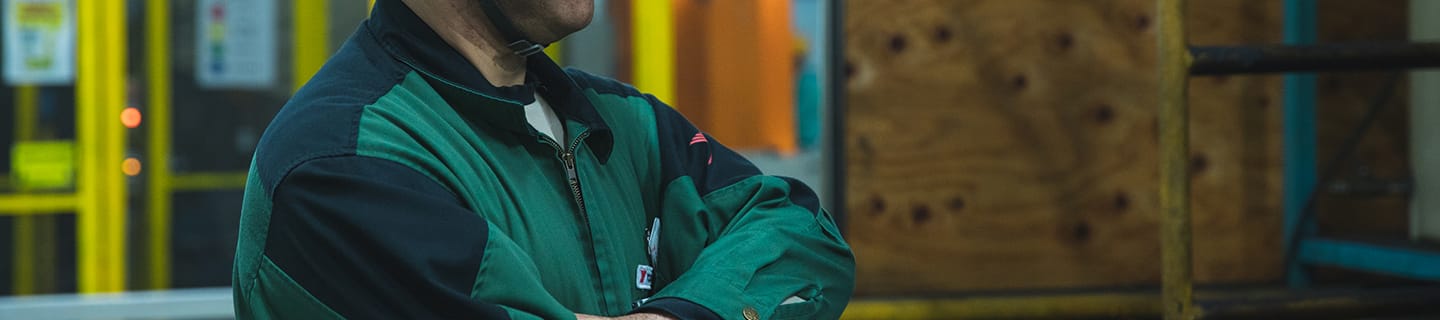
汎用インバータの動作特性の把握に多少手間取ったものの、すべて内製化したことが功を奏し、試作1号機はわずか2週間で完成。三重工場の関係者の皆さまに性能をご確認いただきました。
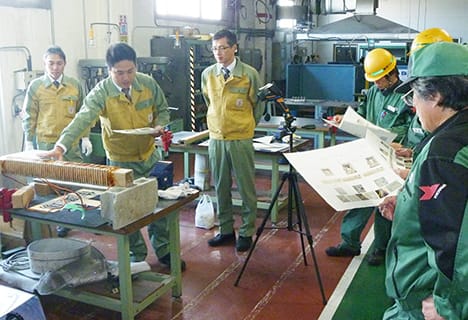
三重工場さまに出向いての試験デモの様子。製造現場スタッフの方々からもさまざまな意見が出された。
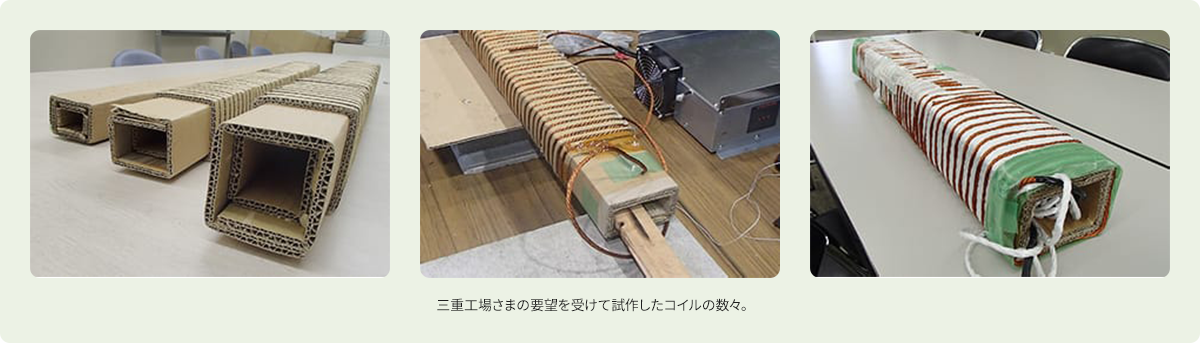
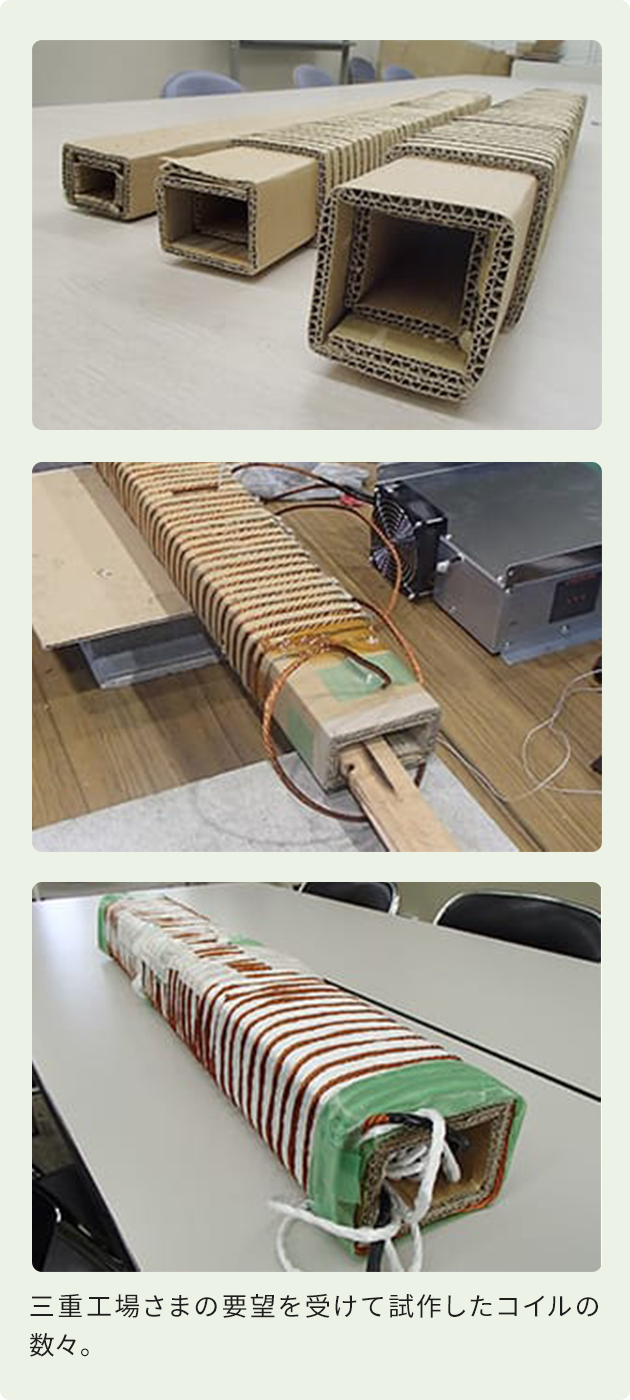
試作1号機ができた後、三重工場さまからは加熱するダイスの本数や収容方法、使いやすさ、安全性など細かな要望が出されました。三重支店を中心に試作を繰り返し、試作したコイルは5号機にまでおよびました。苦労したのはダイスの収納本数や置き方によってコイルの外形が変わるため、加熱特性も大きく変化してしまうこと。
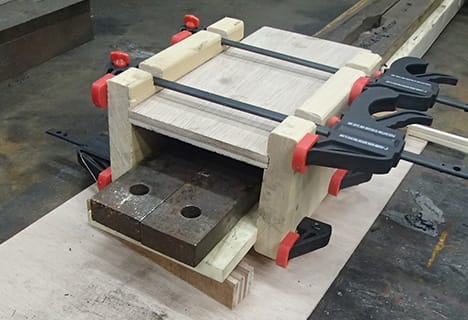
三重工場さまに出向いての試験デモの様子。製造現場スタッフの方々からもさまざまな意見が出された。

中部電力
ミライズ
「三重工場さまのご要望にできる限り早く応えようと、三重支店と本店が一体になって試作と検証を続けました。石川(三重支店)は20回以上も実験施設に足を運んだはずです」
コイル1号機の試作から約4ヶ月でコイルの仕様検討は完了。段ボールを使ったアイデアと製品化への熱意がこの短期化を実現したのです。

横浜ゴム
田所さま
「私たちにとっても生産設備にIH機器を導入することが初めてでしたので、中電さんにはあれこれと注文やお願いを出しました。週末に要求を伝えたら、週明けには手直ししてくれたことも。びっくりするくらいのスピード感でした」
お客さまのために
“まだ世の中にないもの”を
生み出す
コイルの仕様は決まったものの、それはあくまで本体を段ボールでこしらえた試作機でのもの。ここから実際に生産ラインで稼働するIH加熱装置を製造しなければなりません。24時間休まず操業している三重工場さま。その過酷な環境に適した耐久性と安全性、現場スタッフに負荷を掛けない機能性、メンテナンス性など、設計段階からクリアしなければならない課題は数多くありました。

中部電力
ミライズ
「今回のIH加熱装置は、生産設備の一部としてお客さまのものづくりに直接使われるもの。そのコイル設計の内製化は中部電力ミライズとしても初めての挑戦でした。社内に培われてきた技術や情報、人的リソースを使えばできるはずだと自信はありましたが、苦心したことも多かったですね」
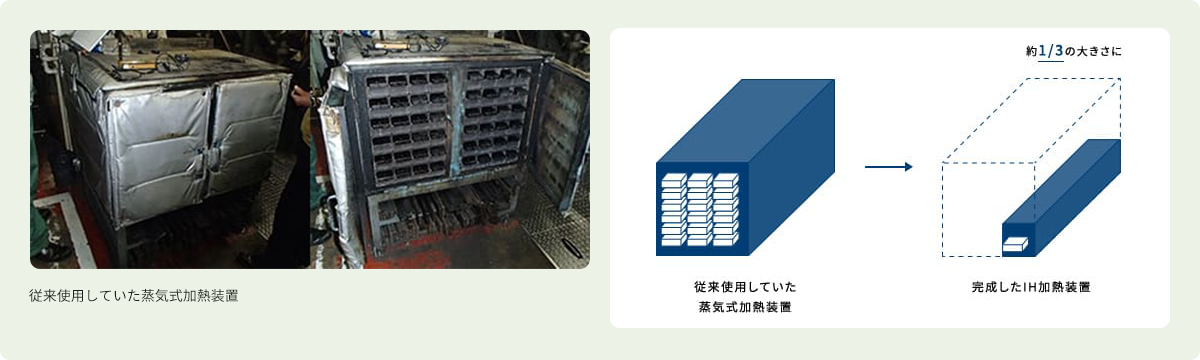
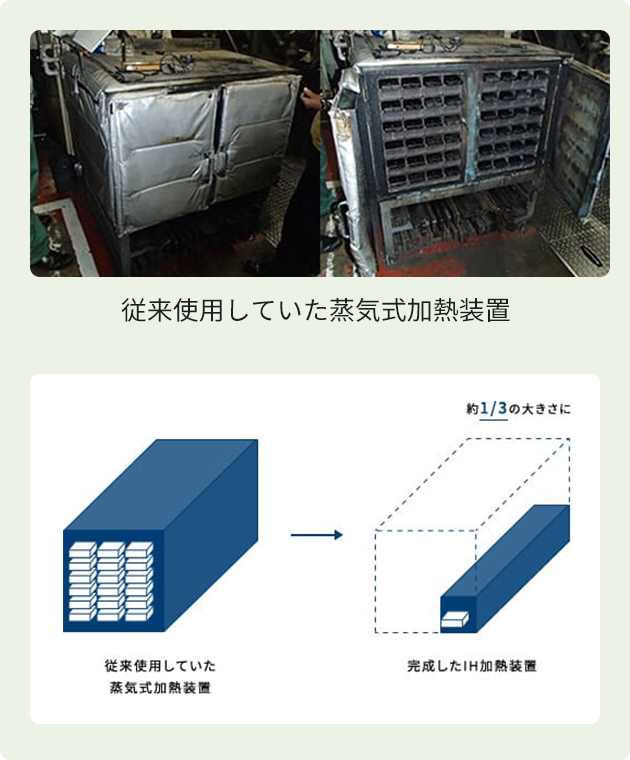
これまで中部電力ミライズでは、メーカの技術や既製品と、中部電力ミライズの持つ情報や知見を組み合わせてお客さま課題の解決提案をおこなってきました。しかし、「開発一体型SO」の目指すものは、お客さまニーズに中部電力ミライズの技術(開発設計)を掛け合わせて“まだ世の中にないもの”を生み出し、お客さまごとに最適なソリューションをお届けすること。
IH加熱に関する技術ノウハウや試験体制などの強みを生かし、設計と並行して進めたユニット材料の選定では、コスト面も考慮しながら耐熱性や絶縁性に優れた素材をリサーチ。生産ラインの後工程との調整もおこなうなどメーカ的な役割も担いました。

中部電力
ミライズ
「産業用機器の設計・開発というテーマに対して、この案件で私たち自身が学んだことも大変多くありました」
数々の要件をクリアしながらユニット全体の仕様や設計図面が決定し、IH加熱装置の実製作は外部の加工会社に依頼。2014年7月に完成し、試運転を経てタイヤ製造ラインの押出工程に導入されました。
大幅な省エネ、
CO2削減に効果を発揮。
同時に製品の品質向上、
作業環境の改善にも貢献
汎用インバータの動作特性の把握に多少手間取ったものの、すべて内製化したこと導入後はダイスの急速予熱が可能になり、従来の蒸気式に比べて加熱に要する時間は1/30(30分から1分)と大幅短縮に成功。さらに、蒸気式で発生していた装置や配管からの放熱、蒸気漏れなどのロスが無くなり、1年間の一次エネルギー使用量は96%削減、CO2削減量は34.9トン削減を実現しました。
また、蒸気式でのダイス予熱では温度が安定しなかったため、原料のゴムを押し出す際に初期段階で「耳切れ」という材料ロスが発生していました。しかし、IH加熱では温度設定が0.1℃単位ででき安定したコントロールが可能。耳切れも大幅に減少し製品の品質向上にも貢献しています。が功を奏し、試作1号機はわずか2週間で完成。三重工場の関係者の皆さまに性能をご確認いただきました。
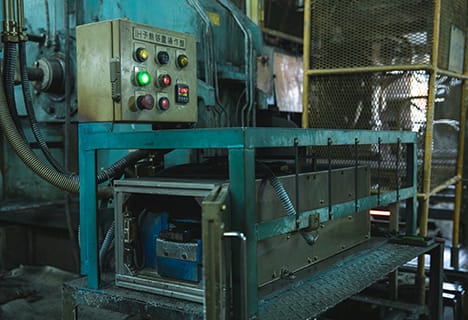
全ラインで12機が稼働するIH式加熱装置。
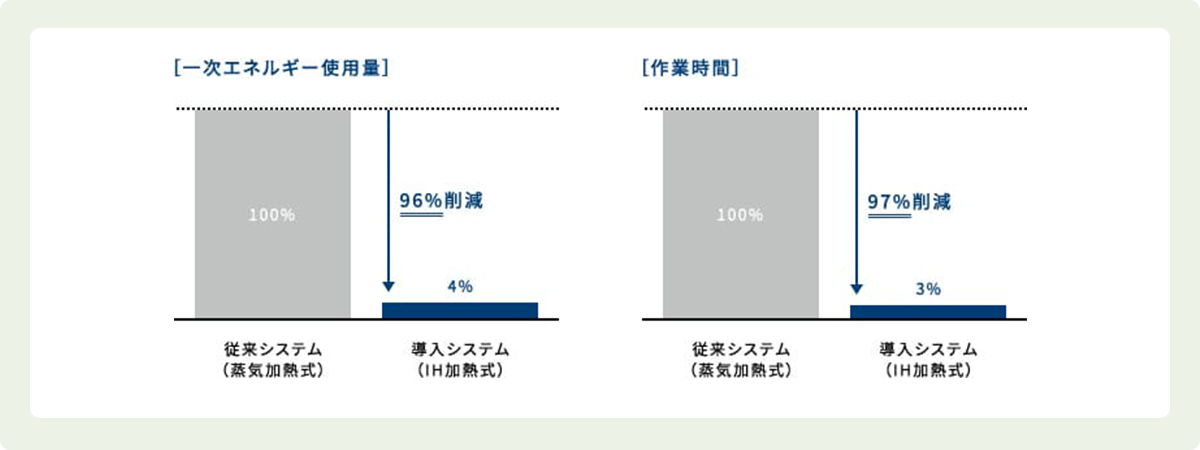
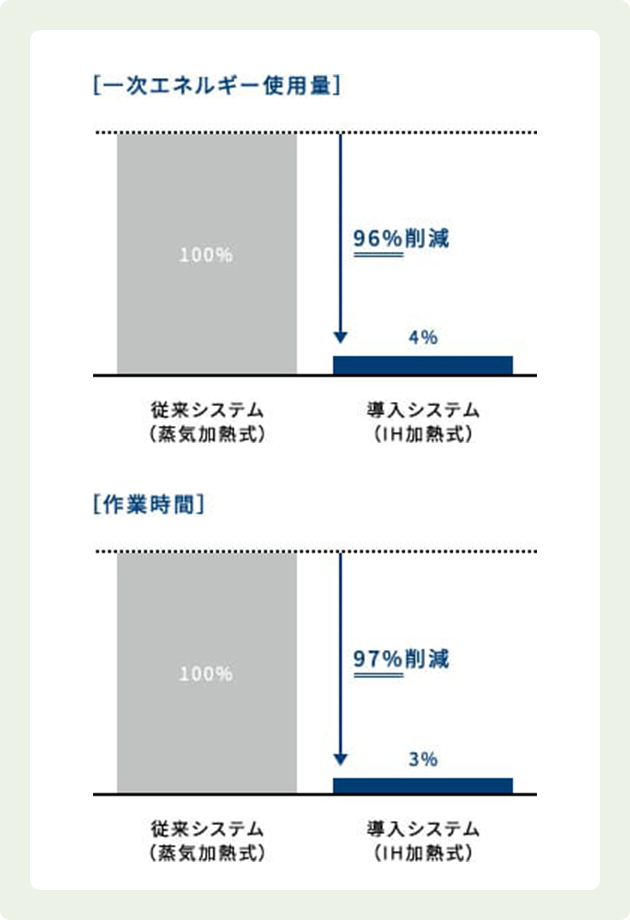
現在では三重工場の押出工程全ラインにおいて計12機のIH加熱装置が稼働中。導入後約5年半が経過していますが大きなトラブルは一度も起きておらず、蒸気熱が無くなったため現場の温度が下がり、作業環境も改善して作業スタッフからも好評とのこと。
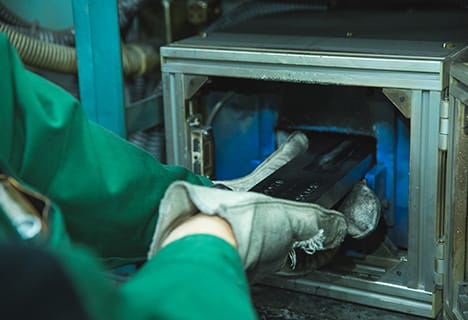
ダイスは使用時に必要な分だけ予熱。設定温度までわずか1分で急速加熱する。
投資効果の高さが評価され、
海外の生産拠点へも
グローバル展開
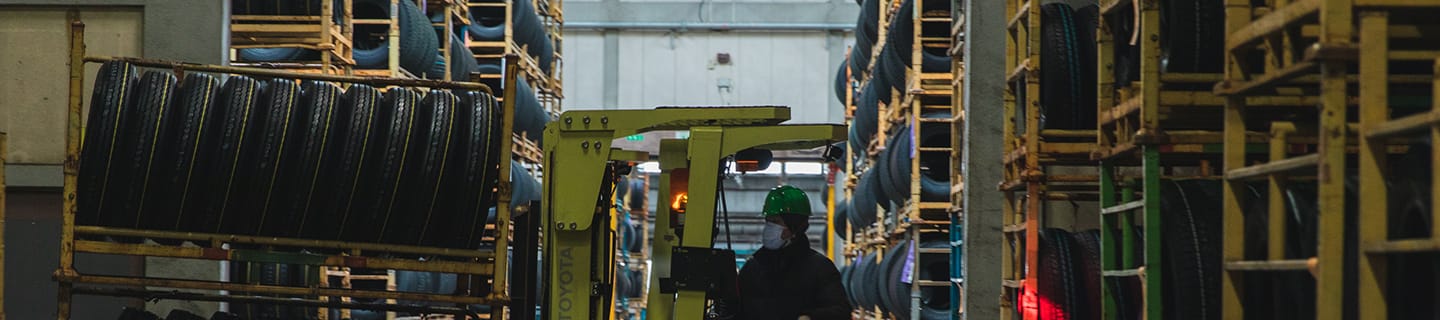
横浜ゴムさまでは三重工場での大きな成果を受けて、同様の製造工程がある工場へのIH式加熱装置の導入を積極的に推進。国内では新城工場(愛知)に4台(さらに追加設置を計画中)、海外では東南アジアの工場を中心に計10数台を導入するなど、この施策は全社的に高く評価されています。
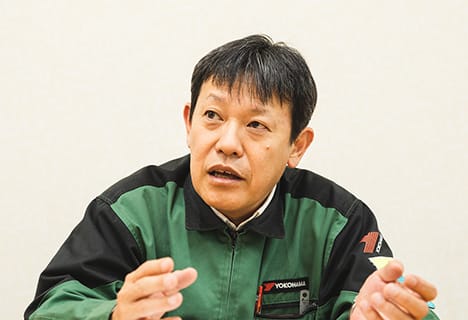
さらなる省エネ推進を目指す工場長の森本さま。

横浜ゴム
森本さま
「当社では各工場でさまざまな省エネや環境対策の取り組みを継続しています。その中でもこのIH式加熱装置の事例は非常に投資効果が大きいです。今後さらに大きな省エネ効果を得るためには、IoTやAIの活用なども必要かもしれないと考えていますし、中部電力ミライズさんにはこれからも色々な面でぜひ力を貸してほしいですね」
現在三重工場さまでは加熱が必要な他の工程でも新たな改善策に取り組み、中部電力ミライズも引き続きお手伝いさせて頂いています。
今後も産業分野のお客さまのニーズを的確にキャッチし、開発一体型SOで生産現場の課題解決に積極的に取り組んでいきます。
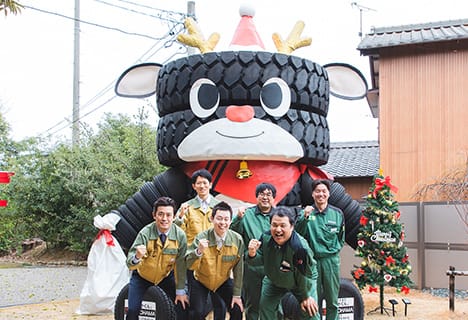
三重工場の設備課の皆さまと中部電力ミライズの担当者たち。
横浜ゴム
田所さま
「段ボールにコイルが巻いてあるのを最初に見た時、大丈夫かな?と思いましたけど(笑)、ダイスは短時間で問題なく加熱して納得できたので、工場内で検討して正式な開発にGOサインが出ました」