お客さまPROFILE
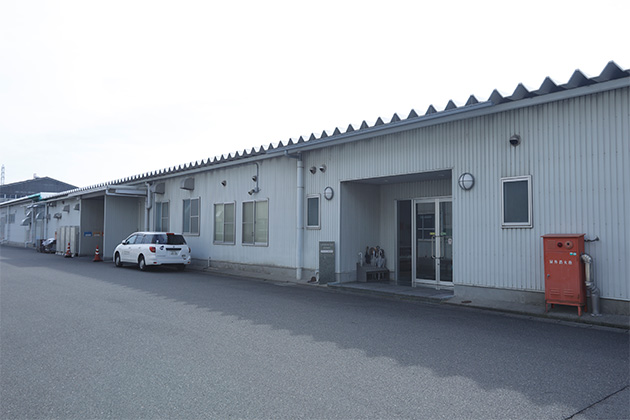
1901年(明治34年)、大理石を中心にした石材の加工・販売を目的に大垣市に創業した老舗企業。同社の大理石は国会議事堂をはじめ、有名な建築物にも多く採用されています。
現在は「建築石材部」「鉄工生産部」「電子生産部」の3事業からなる。鉄工生産部は戦前から鉄道車輛の部品製造を手掛け、1998年に立ち上げられた電子生産部はパソコンなどIT機器の部品製造を手掛けています。
index
取引先の需要動向に左右される
売上構造のため
コスト削減が重要課題に
1901年(明治34年)、大理石を中心にした石材の加工・販売を目的に創業した矢橋大理石株式会社さま。現在は「建築石材部」「鉄工生産部」「電子生産部」の3事業部の構成で、「電子生産部」では、パソコンやスマートフォン、車載用製品など私たちの生活に欠かせない電子回路基板の穴明け加工を中心とした微細加工事業を展開しています。主要取引先は、同じ市内に本社を置き、電子事業・セラミック事業でグローバル展開するイビデン株式会社さま。同社より穴明け加工の生産工程を受託しています。
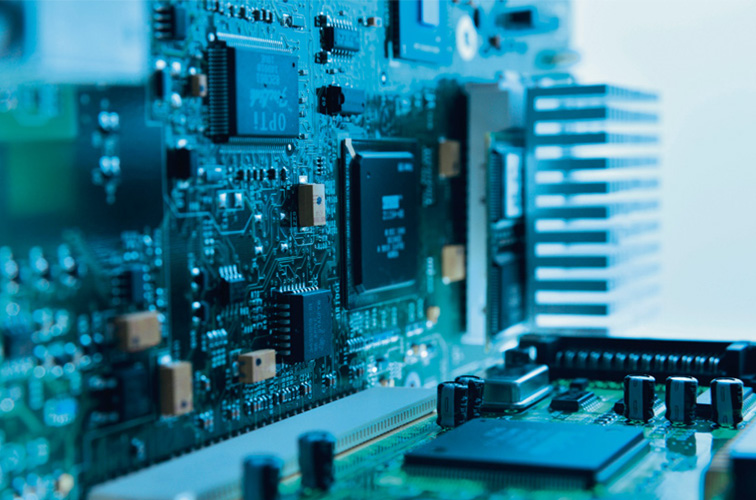
主にパソコンやスマホなどの電子回路基板の穴明け加工を手がけている。
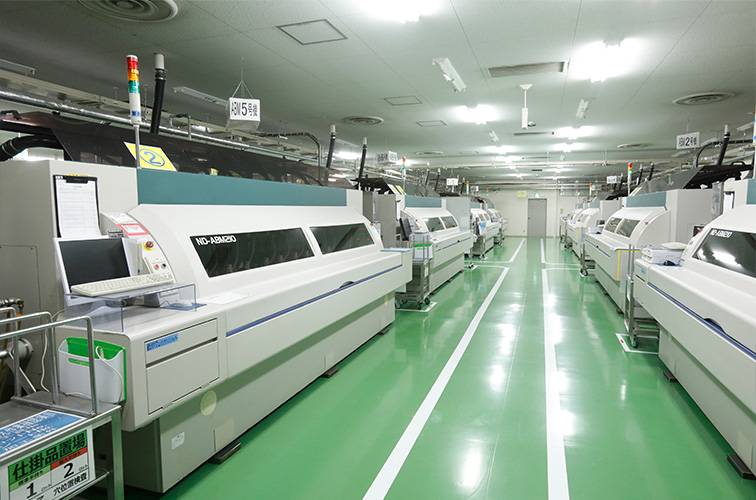
工場内には数十台の大量エアを使用する穴明け加工機が設置され、24時間連続操業。
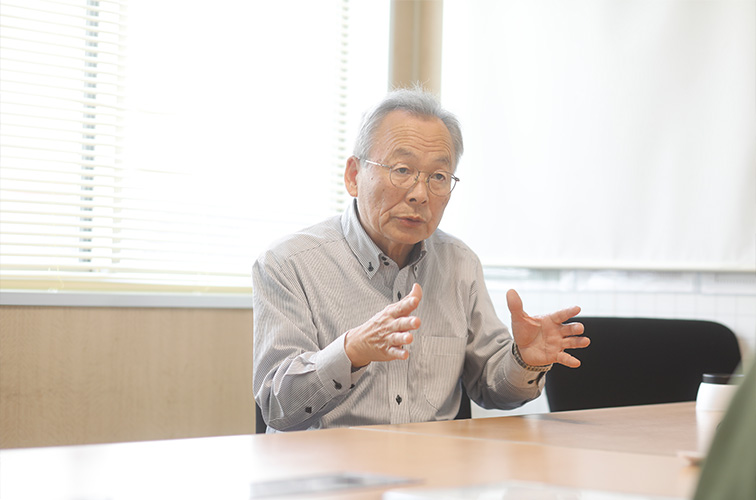
電子生産部部長 浅野常雄さま
電力消費の大半を占める
コンプレッサの運用改善に着手
こうした課題を抱える中、矢橋大理石株式会社さま全体において電気使用量の約85%を占めていたのが電子生産部でした。主要な生産設備である電子基板の穴明け加工機のドリル回転部は、コンプレッサから送気される圧縮エア。現場は24時間連続操業しているため、6台あるコンプレッサも常時運転する必要があり、電気使用量の大半がコンプレッサ設備によるものでした。
電子生産部ではコスト削減策として設備保全チームを中心に、2015年からコンプレッサの運用改善に向けた取り組みに着手。「無駄なエアを出さない」「エア圧力を下げる」の2つをテーマに具体的な改善策を検討しました。
「無駄なエアを出さない」ためには、停止時の穴明け加工機へのエア送気バルブを閉じることを実施。機器メーカーの説明では機器保守の観点から、常時エアを送気し続けることを推奨されていましたが、独自に検証した結果、停止時はエアを止めても、製品品質に影響を与えないことを確認。これにより、電気使用量の約10%削減につなげました。
さらに「エア圧力を下げる」ために、コンプレッサのエア圧力(初期設定値:0.87Mpa)を段階的に引き下げていくことを決断。生産状況や加工機の動作具合などを慎重に見極めながらテストを繰り返し、最終的に0.83Mpaまで引き下げることに成功。同時にコンプレッサの稼働台数も1台停止し、5台で運用できるようにしました。
コンプレッサ1台削減による省エネ効果としては、設備投資ゼロでひと月当たり約100万円のコスト削減を達成。
これら一連の取り組みにより、エネルギー原単位の削減目標も達成し、同社は2016年度「エネルギー管理優良事業者等中部地方電気使用合理化委員会・委員長表彰」を受賞しました。
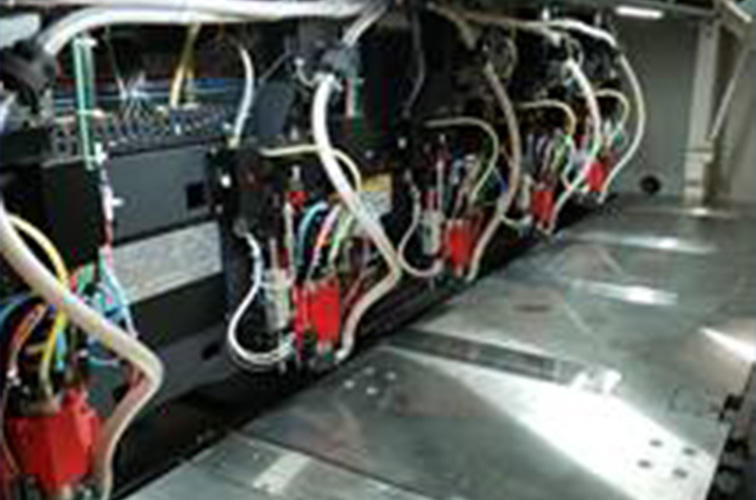
穴明け加工機のドリルは圧縮エアでホバリングによる非接触化させることで、1分間に数十万回転し、基板に数百万以上の穴を明ける。

ドリルの刃先は超微細なミクロン径。
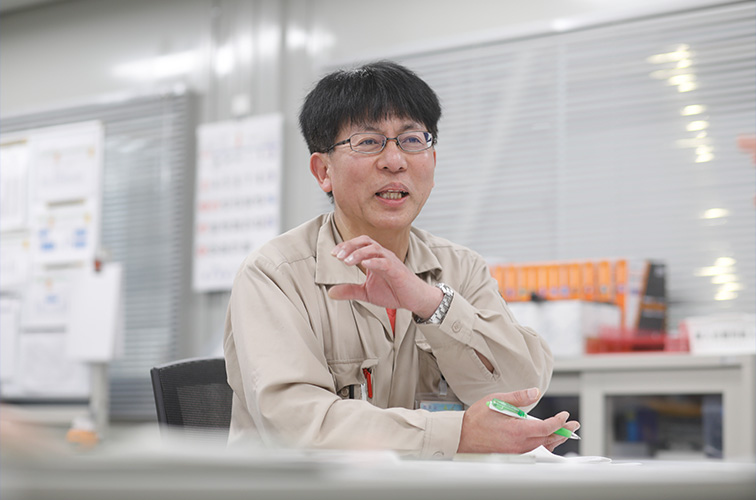
省エネ・コスト削減に取り組む設備保全チームの中心的存在、林直博さま。
「見える化により、コンプレッサの運転状況のトレンドがリアルタイムに分かるので、保守として安心」
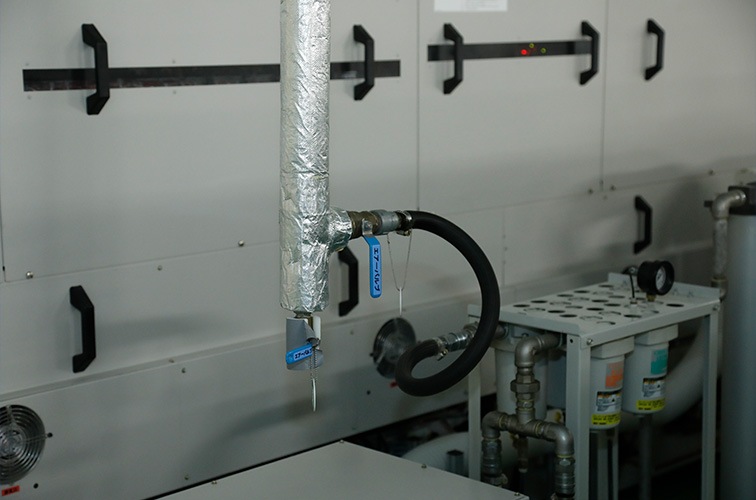
停止時の穴明け加工機は、圧縮エアの送気バルブを閉じ、エアの無駄を減らす。
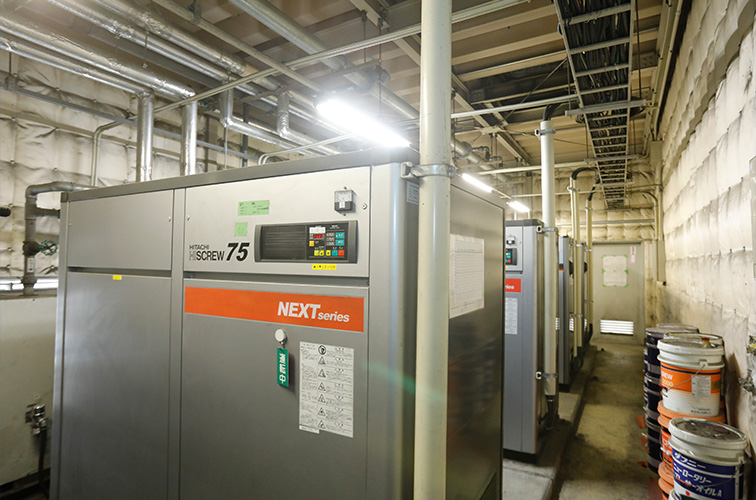
コンプレッサは2つの設備室に6台設置。
「○っとちゅうでん コンプレッサIoT最適運用サービス」の
導入第1号に
「社内努力によって省エネ、省コストについて一定の成果は出ましたが、正直なところ、これ以上の方策は見つからない状況でした」と語るのは、設備保全チームの林さま。
そんな折に当社がご提案したのが「○っとちゅうでん コンプレッサIoT最適運用サービス」でした。
これはコンプレッサ設備に電流および圧力センサーを設置し、電気使用量やエア圧力などのデータを収集機器(ゲートウェイ)を介して常時接続されたインターネット経由で中電のクラウドサーバに常時収集することにより、コンプレッサの運転状態が、担当者のパソコンやスマホ画面でいつでも、リアルタイムに「見える」というサービスです。
また、収集したデータを分析することで、より効率的な運用や設備の最適化など改善を図ることが可能です。

矢橋大理石
さま
「次の手立てが無い中でタイミング良く提案いただけましたので、まさに渡りに船でした」
2018年8月、このサービスの最初の導入先として、矢橋大理石さまに見える化の設置工事を実施しました。
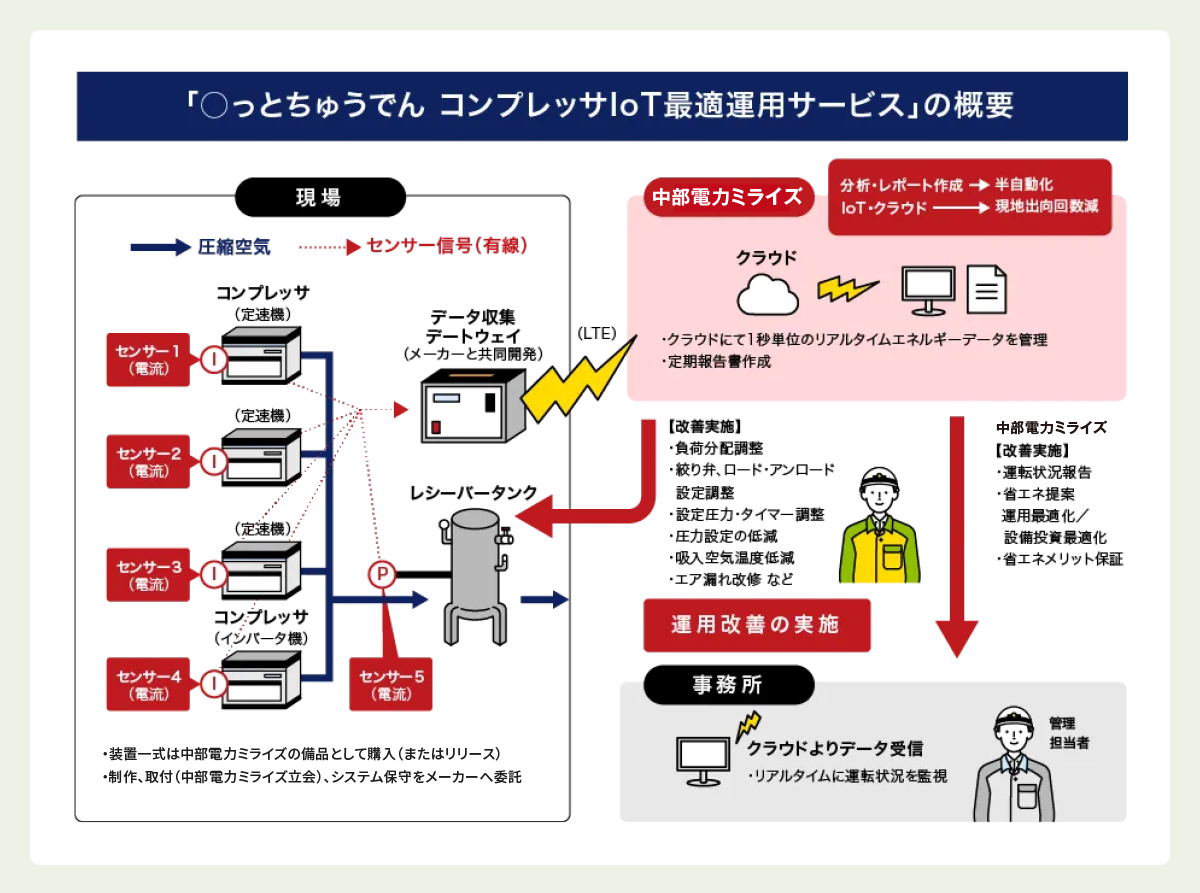
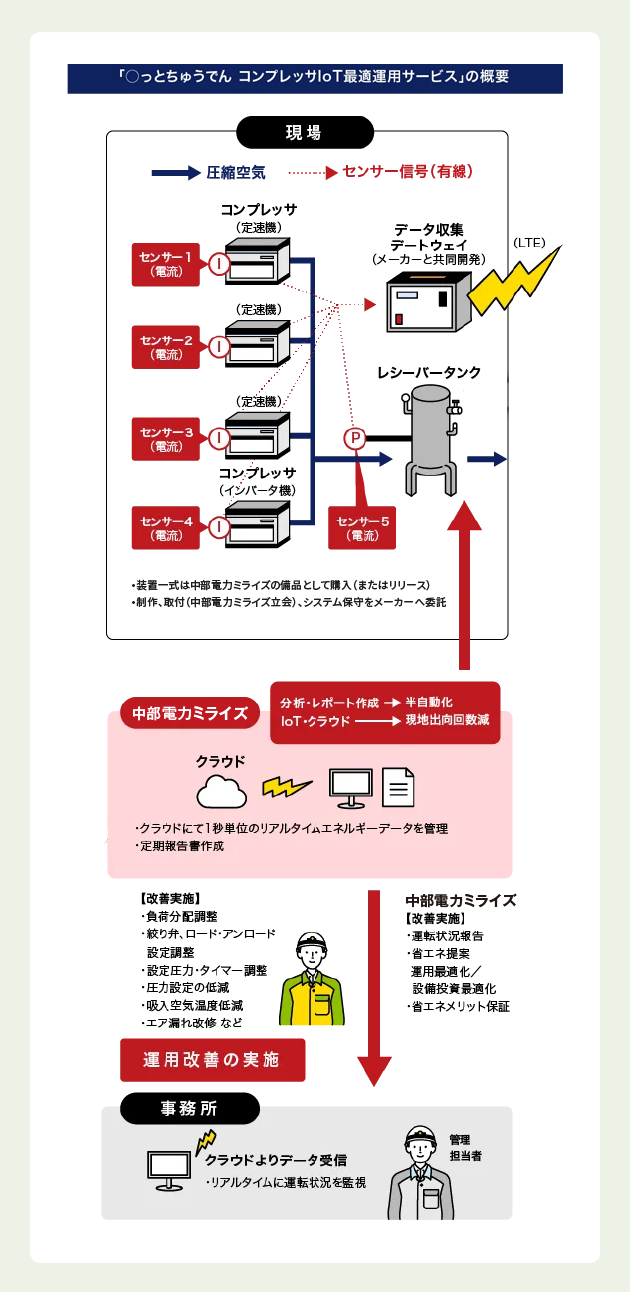
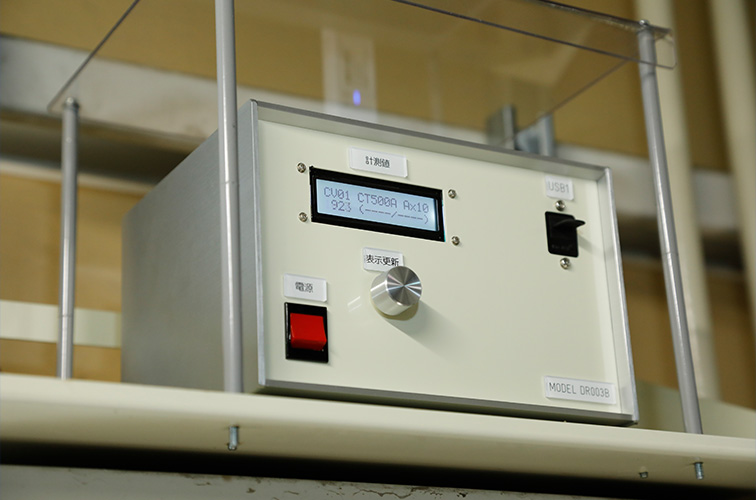
データ収集ゲートウェイ本体はルータ機能を持つ。常時インターネット接続され、クラウドサーバにリアルタイムでデータをアップロード。
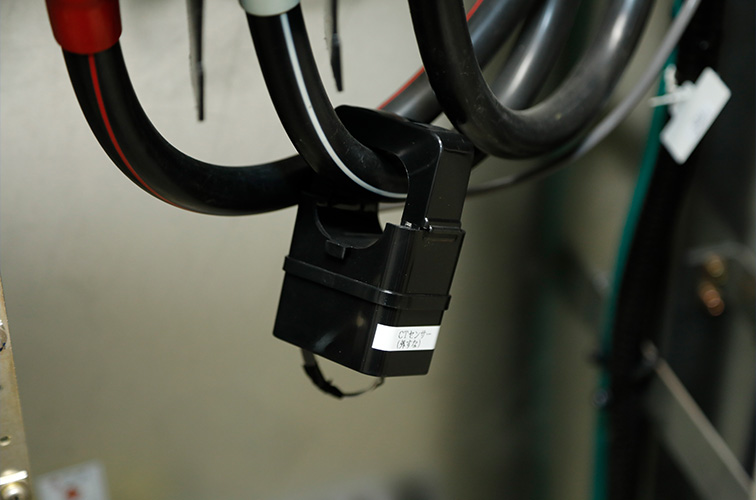
コンプレッサ電源ケーブルに取り付けられた電流計測用CTセンサー。データ収集ゲートウェイにつながっている
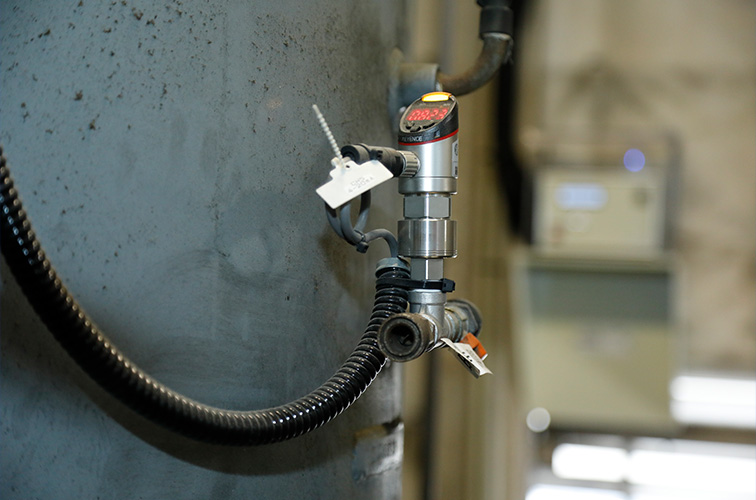
圧縮エアのレシーバータンクには圧力センサーを設置。これもデータ収集ゲートウェイと接続。
運転状態の「見える化」は
効果絶大。
コンプレッサ稼働台数をさらに1台減らし、
さらなるコスト削減を実現!
これまでは現場にいかないと分からなかったコンプレッサの運転状態が、このサービスの導入により離れた場所からもリアルタイムで監視できるようになりました。

矢橋大理石
さま
「エア圧力や電気使用量が数字やグラフで分かりやすく「見える化」されるので、これまで試行錯誤していたエア圧力の調整も非常に安心しておこなえるようになりましたね」
設備保全チームではそれらのデータを精査し分析。生産現場と連携してコンプレッサのより最適な運転を模索し、エア圧力を0.83Mpaからさらに下げ、0.815Mpaでの加工機の正常稼働を可能にしました。
コンプレッサの設定圧力変更前後の
運転状態の違い
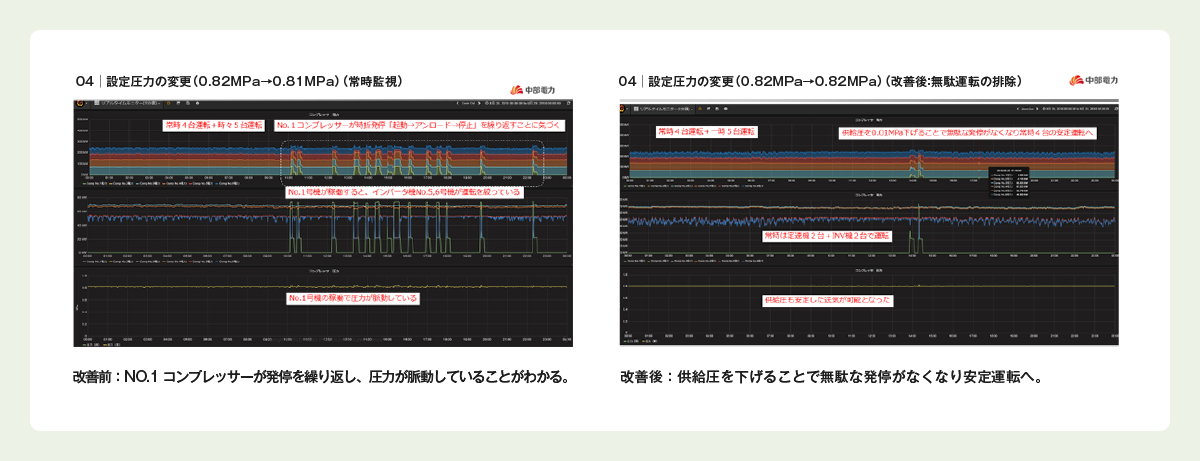
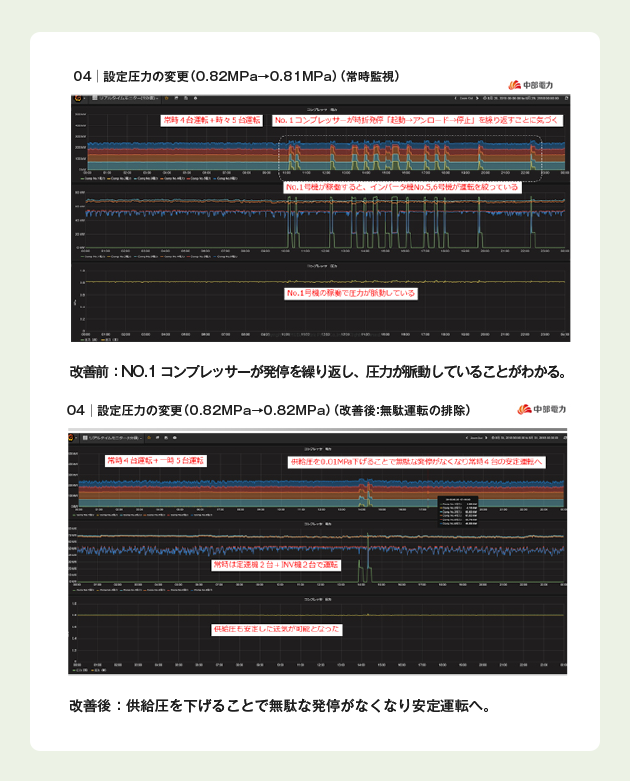
設置1ヶ月後、当社から「○っとちゅうでん コンプレッサIoT最適運用サービス」のご報告を実施した際には、コンプレッサのエア圧力変更による効果試算(240万円/年)や運転方法の一層の最適化策として、定速機の優先運転をご提案させていただきました。
その後、電子生産部さまでは、穴明け加工機増設に伴うエア配管延長により、エア圧力を再度0.83Mpaに運用を戻すともに、コンプレッサ2台を高効率・高出力タイプに更新しました。
運用変更や設備更新後も、運転状態の「見える化」を継続実施して、最適な運用方法を検討してきました。
その結果、優先運転するコンプレッサを高効率機に変更をするとともにエア圧力を見直したことでエア圧力0.815Mpaまで下げることができ、コンプレッサをもう1台停止することにも成功しました。
当初の6台稼働から、生産設備が増えたにも関わらず、延べ2台停止することができ、4台稼働で運用できる体制を実現。コスト削減効果も非常に大きく、約20%の省エネ、省コストを実現。今後の需要動向に寄りますが、見える化により、更なるコスト削減を目指し運用改善を実施しています。
また、サービス導入当初に設備保全チームから、「圧力変動や設備停止トラブルなどが起きた時に、現場を離れていても、すぐに「気づき」が得られるよう、アラートメールが送信される仕組みができないか」という依頼をいただきました。この要望に対して、機器をカスタマイズしてご提供することで、現場からは「コンプレッサ停止のアラートメールのおかげで加工機の運転状態も迅速に分かるようになり、保全面で大変助かっている」とご活用いただいています。

矢橋大理石
さま
「中部電力ミライズさんから提案をいただいていっそうのコスト削減ができたことは、経営層からも高く評価されています」
当社では複数台のコンプレッサを運用されているお客さまを中心に、「○っとちゅうでん コンプレッサIoT最適運用サービス」を積極的にご提案していきたいと考えています。
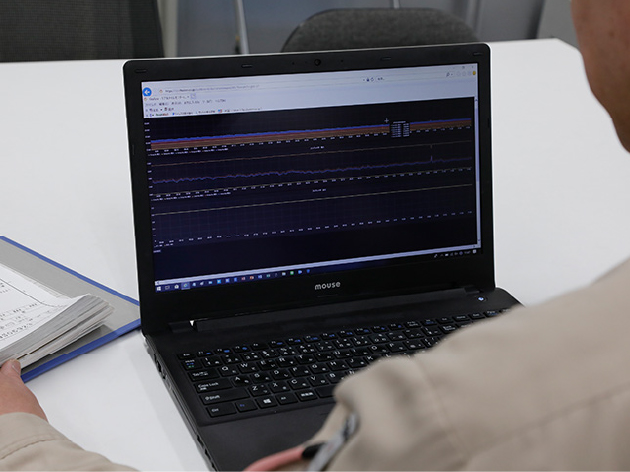
現場にいかなくてもパソコンやスマホで運用状況がいつでも「見える」。
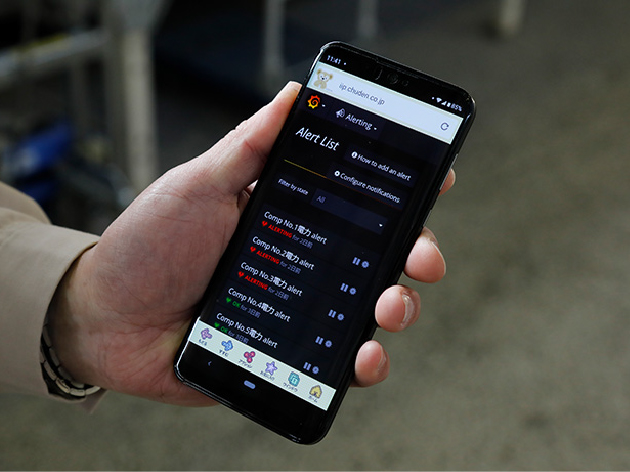
運用後に追加された「アラートメール送信機能」。
矢橋大理石
さま
「当社電子生産部の売上は、先方の生産品の需要動向にどうしても左右されてしまうため、生産現場でのコスト削減は常に取り組むべき重要課題です」